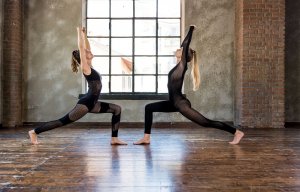
Warp knit seamless specialist Cifra launches new website
Paid content
How drives, motors, and PLCs are transforming textile production processes. By Umit Kahraman, Global Machinery Segment Manager at ABB.
7th March 2024
Innovation in Textiles
|
Zürich, Switzerland
The textile industry faces a diverse range of challenges, including rising energy costs, complex production processes, evolving consumer trends, and a growing emphasis on sustainability.
In response, the industry is embracing digital technologies like automation and the Internet of Things (IoT) to transform its operations. These technologies are being utilised to optimise production processes, enhance supply chain management, offer customised products, and enable real-time monitoring and control.
However, despite the potential for growth in this area, only around one-third of textile facilities have integrated automation into their production cycles. This highlights the significant opportunity for growth and the importance of streamlining and optimising textile machines.
As sustainable fabrics and practices gain more popularity and companies prioritise reducing their carbon footprint, the need to enhance energy efficiency while increasing production velocity will become even more urgent. This can be achieved through integrating high-efficiency motors, variable speed drives (VSDs), and programmable logic controllers (PLCs) in textile machines.
Using high-efficiency motors and drives to optimise energy consumption
In recent years, we’ve seen a growing industry-wide commitment to sustainability throughout the production process, including adopting renewable materials and improving energy efficiency. Textile companies are setting specific sustainability targets, responding to increasing customer demands for transparency in smart and sustainable practices.
As a result of the focus on process optimisation, there has been greater investment in high-efficiency motors, such as IE4 or IE5 synchronous reluctance (SynRM) models. These modern motors have already shown they can play a pivotal role in helping to minimise energy usage.
Variable speed drives, also known as variable frequency drives or, simply, drives, are also central to this energy optimisation process. They allow for adjustments in motor speed and torque, giving operators precise control over specific textile applications.
The conscious bid for high-efficiency equipment is being further reinforced by regulatory obligations, such as the Ecodesign Directive, which has provided further impetus to the uptake of these motors and drives.
However, it’s also true that many textile companies are sticking to old processes due to cost concerns. In many cases this is understandable, but it’s based on a somewhat false economy: the higher cost of more efficient technology can often actually be recuperated in a short period, sometimes even a matter of months, purely through energy savings.
Increasing productivity through PLC automation
While motor-drive systems can offer substantial energy optimisation opportunities, they should be paired with Programmable Logic Controllers (PLCs) to fully enhance productivity.
PLCs coordinate the activities of drives and motors, ensuring an efficient production line while reducing unnecessary manual intervention. Increased automation, therefore, translates to enhanced output and reduced downtime – two key components for finding a competitive edge in the market.
Added to that, the combination of motor-drive systems and PLCs ensures complete operator control, streamlining operations and fostering a production environment that can be adapted where needed.
Take, for example, a typical contemporary textile manufacturing operation. Here, PLCs control spinning machines, maintaining exact yarn tension, and overseeing weaving processes for a synchronised production line. Further down the line, they automate chemical additions in the dyeing and finishing stages, ensuring optimal conditions for consistent colour and texture. They also help streamline production in cutting, sewing, and quality control processes, as well as coordinating and automating defect sorting.
These improvements indicate why the combination of motors, drives, and PLC automation is becoming crucial for individual companies – and the functioning of the entire textile industry.
How digitalisation can improve reliability
Increased digitalisation is also transforming the reliability of textile machinery. A practice that is gaining popularity is remote condition monitoring, which involves the use of sensors integrated into motors controlled by drives. This allows for real-time monitoring of performance and enables the early detection of potential issues. It also opens up the possibility for predictive maintenance – a proactive approach that tackles issues before they lead to equipment failure.
For a high-demand industry like textile production, where many machines are often running constantly, this is a crucial innovation. Not only does digitalisation ensure energy is being used efficiently, but it also helps companies produce better maintenance outcomes and eliminates the risk of unplanned downtime.
Protecting motors, drives, and PLCs in hot, damp environments
The move towards high-efficiency motors, drives, and PLCs isn’t without its challenges. Of particular concern is how to protect the machinery’s complex components, which are vulnerable to the harsh conditions found in manufacturing facilities.
Considering this, the industry has taken measures to shield these components from undue wear and tear. One common practice is the strategic housing of motors, drives, and PLCs in separate, protective cabinets. Beyond just physical partitioning, air conditioning systems are often used to moderate temperatures and ensure optimal machine performance and longevity. In some instances, entire rooms are set aside with dedicated air conditioning systems.
These protective strategies illustrate the industry’s commitment to overcoming production challenges while protecting vital components, thereby guaranteeing the smooth operation of textile production.
Case study: How high-efficiency drives, motors, and PLCs are transforming textile manufacturing
The development of this technology, then, is already having an outsized impact on the textile industry. One example is Dilmenler Textile Machinery, a global dyeing, and finishing equipment manufacturer, which partnered with ABB more than a decade ago to integrate drives and PLCs in its machinery.
Since then, ABB has helped Dilmenler enhance the robustness and efficiency of its machines and streamline its production process. As a result, textile companies with pressing time schedules have relied on Dilmenler’s machines to offer the best automation solutions available. ABB’s specialised software has further optimised drive deployment, ensuring flawless operation.
Dilmenler’s General Manager, İsmail Şengüller, applauded the total value ABB’s high-efficiency drives, motors, and automation solutions added to the company’s operations and the consistent support offered by ABB. As a result, Dilmenler was able to reduce downtime, improve efficiency, and deliver reliable, high-performance machines to its customers across the globe.
With increased digitalisation and automation in its operations, allied with high-efficiency motors and drives, companies need to mirror Dilmenler’s approach. It’s then that the whole textile sector will reap the benefits.
For further information, please contact:
Umit Kahraman
Global Machinery Segment lead, ABB Motion Drive Products
+358102258772
Business intelligence for the fibre, textiles and apparel industries: technologies, innovations, markets, investments, trade policy, sourcing, strategy...
Find out more