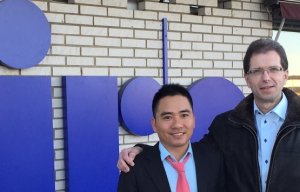
TMAS to support Vietnamese textiles industry
Both companies are at the forefront of sustainable and Industry 4.0-enabled technologies
5th December 2019
Innovation in Textiles
|
Sweden
Swedish textile machinery association TMAS is welcoming two new companies – both at the forefront of sustainable and Industry 4.0-enabled technologies – to its membership.
A new benchmark for embroidery
The first is Coloreel, the developer of a thread colouring unit which enables the instant and high-quality colouring, fixation, washing and lubrication of thread to take place simultaneously to the actual embroidering of a fabric, representing a bold and entirely new approach to this traditional field.
Based on a CMYK ink system, Coloreel’s advanced colorization software and instant thread colouring technology allows a single needle to carry out what previously required multiples of them, and with much more consistent stitch quality.
Designed to work with any existing industrial embroidery machine without modification, the stand-alone Coloreel unit provides complete freedom in the creation of unique embroideries, imposing no limitations on the number of customized colours employed in designs. It allows set-up and lead times to be reduced as well as significant flexibility in production schedules, while eliminating the need for large thread inventories.
With fewer trims required for colour changes, the Coloreel unit can also reduce the total production time required for complex designs by up to 80%, as well as instant reaction to the specific colour requirements of customers.
“Our system is allowing customers to achieve colour effects that have never been seen before – and at a new level of efficiency,” says Magnus Hellström, VP Sales & Marketing at Coloreel. “We are setting the new benchmark for the embroidery industry and we are pleased to join TMAS to help us spread the word.”
Sustainable fabric dyeing
Meanwhile, the second new TMAS member, imogo, has been working to provide much more sustainable fabric dyeing than has until now been possible.
In January 2020 the company will open up its new showroom in Borås, Sweden, in order to fully demonstrate to customers how its patent-pending FlexDyer process provides opportunities for major savings in water, energy, chemicals and dyes, as well as in maintenance and labour.
Its combination of high-speed spray application and a special autoclave fixation step enables flexible output at considerably reduced costs, and what makes it truly flexible is the range of fiber types and blends it can accommodate.
Imogo’s Mini-Max spray test unit for the achievement of offline ‘right first time’ results for the company’s industrial scale Dye-Max will also be installed at the Borås showroom.
Dye-Max spray dyeing technology can slash the use of fresh water, wastewater, energy and chemicals by as much as 90% compared to conventional jet dyeing systems.
“The Dye-Max application unit is based on a closed chamber containing a series of spray cassettes with precision nozzles for accurate and consistent coverage,” explains imogo’s founding partner Per Stenflo. “This works in combination with our patented pro speed valve that controls the volume to be applied.”
The savings in treatment water the Dye-Max achieves are due to the extremely low liquor ratio of 0.3-0.8 litres per kilo of fabric and at the same time, the low liquor ratio and the spray process require considerably less auxiliary chemicals to start with.
All of the water is used in the process, which also greatly reduces the production of wastewater, with only 20 liters being required for wash at changeovers. The low liquid content in the fabric meanwhile minimizes the energy required for fixation.
The Dye-Max has a working speed of up to 50m/min with the practical speed determined by the fabric weight and application volume.
The Spray Applicator can also be incorporated in existing lines to replace a padder, both for dyeing and applying finishing chemistry, in order to increase their productivity and reduce the environmental footstep of existing processes.
Awards
Both new TMAS companies have already received awards for their technologies. Coloreel has claimed the SKAPA prize – Sweden’s largest innovation award – as well as recognition from Texprocess. Imogo has been selected as one of Hello Tomorrow’s Deep Tech Pioneers, received a Vinnova innovation grant and been awarded the Seal of Excellence by the European Commission for its FlexDyer project.
“We are happy to welcome these two exciting companies to our industry and the TMAS association,” says TMAS Secretary General Therese Premler-Andersson. “Both are making important contributions to the industry’s sustainable future with completely new technologies on the market. They improve efficiency and quality and reduce waste in their production processes – benefits that are in line with the expectations for the textile production of the future.”
“It is no coincidence that these newcomers are from Sweden. Our focus on sustainable solutions goes a long way back and is boosted by a very good innovation climate. These are interesting times, with big Swedish companies such as IKEA and HM pushing for sustainable production methods and materials, and this ensures we at TMAS are constantly on our toes to stay on top with innovation.”
Business intelligence for the fibre, textiles and apparel industries: technologies, innovations, markets, investments, trade policy, sourcing, strategy...
Find out more