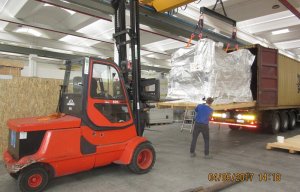
Large project paves the way for Prodye-R
At ITMA, the Karl Mayer Group will be showing solutions for the topics that move its customers, form 8-14 2023, at the Fiera Milano, in Hall 4 B119.
8th June 2023
Innovation in Textiles
|
Obertshausen, Germany
The Karl Mayer Group will be presenting the Multi-Matic 32 Compact as a highlight in the warp preparation sector at ITMA this week. The new warp sampling machine is more than twice as productive as the previous model with the same space requirement, and with simple, fast pattern changes and short setup times, enables the company to react flexibly to the needs of the market. The fully automatic model with optimised ergonomics can also be operated safely despite a shortage of skilled workers.
Link-Matic
Another solution for more customer benefit is the Link-Matic system. With this sophisticated automation solution, the batch changes on indigo and sizing machines can be simplified considerably, thus increasing productivity. An increase of up to 30 % is possible, depending on the number of batches. In addition, there is up to 600 m less yarn waste per batch and less personnel is required. When changing batches, only one operator is needed to prepare the warp beams for feeding into the machine. A fully automatic knotting unit couples the warp yarns of the new batch to the yarns of the batch just finished.
In warp preparation, too, networking the machines with the cloud ensures efficient access to machine data and remote service. In addition, quality management reports can be called up on any mobile device via the cloud, and the prerequisites for a proactive warping cloud function are created. Details are available during a screen presentation.
Bluedye
The Karl Mayer Group is presenting a highly innovative solution for the denim sector which ensures greater sustainability and lower costs. The nitrogen-based dyeing technology Bluedye minimises the immense amounts of water and chemicals used. The need for hydrosulphite and caustic soda - the main environmental polluters of the process - can be more than halved and the volume of water required can also be significantly reduced. In addition, less yarn waste is produced. Bluedye thus scores equally in terms of environmental protection and costs. Operating costs can be reduced by up to 20 %.
The Bluedye on the stand is the first machine in the Karl Mayer Group's new Blueline category. The innovative industry leader is committed to a more sustainable and environmentally friendly textile industry. From now on, it will list all its machines and solutions that make a proven contribution to sustainability under the Blueline category.
Business intelligence for the fibre, textiles and apparel industries: technologies, innovations, markets, investments, trade policy, sourcing, strategy...
Find out more