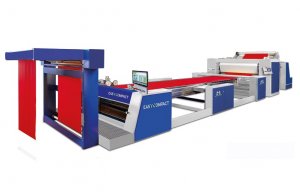
New Easy Compact for open width knitted fabrics
Faults in product development can be expensive for clothing manufacturers, researchers for the Hohenstein Institute report. Inconsistencies in the materials, pattern, workmanship and function in the creative design process are said to put the efficiency of measuring the quality control at risk, due to the lack of central procedure for documentation or process monitoring. As part of a research project, scientists at the Hohenstein Institute in Boennigheim have been looking at the QM tools that would be appropriate for the short and creative product development cycle that occurs in the clothing industry. Project manager Simone Morlock commented: “Our aim was to find a solution that is really geared towards the processes and the demand for creativity in the clothing industry, as well as what was possible from the point of view of organisation and timescales.”
18th December 2013
Innovation in Textiles
|
Boennigheim
Faults in product development can be expensive for clothing manufacturers, researchers for the Hohenstein Institute report. Inconsistencies in the materials, pattern, workmanship and function in the creative design process are said to put the efficiency of measuring the quality control at risk, due to the lack of central procedure for documentation or process monitoring.
As part of a research project, scientists at the Hohenstein Institute in Boennigheim have been looking at the QM tools that would be appropriate for the short and creative product development cycle that occurs in the clothing industry.
Project manager Simone Morlock commented: “Our aim was to find a solution that is really geared towards the processes and the demand for creativity in the clothing industry, as well as what was possible from the point of view of organisation and timescales.”
Quality management figures show that about 75% of all product faults originate in the development phase. However, 80% of those defects are only discovered and corrected at later stages of the work - and, according to the so-called Rule of Ten, the cost of correcting faults increases by a factor of 10 at each stage, from development through production to the end-user.
If the fault is only detected by the customer, then the cost of correcting it can be far exceeded by the additional damage to the image of the product.
The sooner quality control starts, the greater the effectiveness, the scientists believe. However, whereas in other sectors, especially the automotive industry, established procedures for preventive quality control during product development are already in place, these are very little used in the clothing industry.
In many companies, the development processes tend to be rather unstructured. Many things happen at short notice. It is by no means always the case that there is a systematic flow of information back to the design department, for example, following analysis of the returns from the previous season.
The project identified some ways in which the clothing industry could improve. Among other things, checklists have been developed which can be used to test models when they have been designed, systematically and preventively, and before the subsequent manufacturing process, such as the production of prototypes, begins. This means that faults can be effectively avoided.
The series of workshops took place, initiated by the project with the aim of introducing quality-assured product development through the PDM/PLM and ERP systems that are familiar within the industry. The workshops were attended by well-known clothing companies producing functional clothing, underwear, workwear and high-fashion garments, as well as by well-known providers of ERP, PDM and PLM systems for the industry.
This close cooperation meant that both the requirements of the clothing manufacturers and the options and possible solutions put forward by the software providers could be discussed. Simone Morlock commented: “With quality-controlled product development, quality-related costs can be significantly reduced.”
Business intelligence for the fibre, textiles and apparel industries: technologies, innovations, markets, investments, trade policy, sourcing, strategy...
Find out more