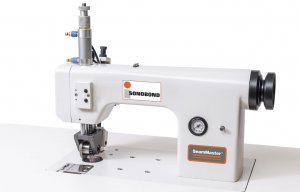
Sonobond becomes part of Inductotherm
The result of the new machine line is ultra-reliable seams achieved up to four times faster than with conventional sewing machines.
18th July 2014
Innovation in Textiles
|
West Chester, PA
Sonobond Ultrasonics, a leader in the application of ultrasonic bonding and welding technology, has been awarded trademark registration for its complete line of ultrasonic ‘sewing’ equipment that bonds nonwoven and woven synthetic materials.
The units are now known as SeamMaster Ultrasonic Sewing Machines. They include general purpose and high profile models, table-mounted cutter/sealer units, and modules for original equipment manufacturers.
Though comparable in appearance and operation to traditional sewing machines, Sonobond’s equipment uses ultrasonic vibrations, instead of needles, thread, glues or other adhesives, to bond materials that are synthetic or blends containing up to 40% natural fibres.
The machines use a patented rotary operation, where both horn and pattern wheel rotate at the same time to cut, sew and trim in one pass.
The result is ultra-reliable and soft-to-the-touch seams achieved up to four times faster than with conventional sewing machines and 10 times faster than with adhesive methods, enabling some manufacturers to boost their production output, the manufacturer reports.
Sonobond introduced its first SeamMaster Ultrasonic Sewing Machine in October 1991 to meet demands for safer medical garments, such as gowns and face masks, and disposable items, including mattress covers, surgical wipes and wound dressings.
“Due to its reliability in producing bonded edges and secure seams without stitch holes, glue gaps, fraying or unravelling, the first SeamMaster Ultrasonic Sewing Machine met tough OSHA regulatory requirements for barrier seams,” Melissa Alleman, Vice President, explained.
The SeamMaster High Profile Ultrasonic Sewing Machine is currently Sonobond’s most popular model due to its large pattern wheel, high clearance and ability to accommodate bulky materials and hand-guided operations with tight tolerances and curves. The machine is used by most major manufacturers of body armour to seal the outer nylon shell of ballistic vests and produce a reliable bond.
The SM10 Ultrasonic Cutter/Sealer model is a table-mounted unit with a 16” x 20” operating area and an easily interchangeable pattern wheel located in the centre.
It can handle a variety of patterns up to 10mm wide, slitting and sealing two layers of material and eliminating fraying and unravelling along the sealed edge. Faster than either conventional sewing or adhesive machines, it operates at speeds of up to 60 feet per minute, the company reports.
In the textile and apparel industries, Sonobond units have been used for slitting, embossing, lace making and stitching. The machines are used to assemble draperies, window shades, awnings, blankets, tablecloths, pillows, athletic accessories, carpets, banners, flags, aviation insulation panels, netting, ribbons, and all types of garments.
SeamMaster Ultrasonic Sewing Machines have even been used by Cornell University fashion design students to create functional or decorative details. Manufacturers of oil containment booms have found the Sonobond machines essential for producing inner polypropylene boom socks with seams strong enough to support an eight- to ten-fold increase in weight due to oil absorption.
Additionally, filter manufacturers have used the equipment to make custom and specialty bags, sleeves, pads and other filtration products for the chemical/pharmaceutical, automotive, environmental, food/beverage and manufacturing industries.
Business intelligence for the fibre, textiles and apparel industries: technologies, innovations, markets, investments, trade policy, sourcing, strategy...
Find out more