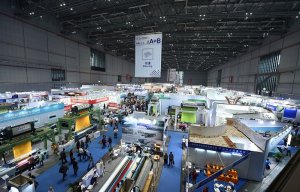
New dates for ITMA Asia + CITME 2018
His name is Assistant Q and in addition to his technical know-how he offers absolute loyalty and commitment, the manufacturer reports.
15th September 2016
Innovation in Textiles
|
Uster
Uster Technologies, a leading high-technology instrument manufacturer, is offering spinners a new virtual staff member to make a real difference in quality management and business.
His name is Assistant Q and in addition to his technical know-how and expertise he offers absolute loyalty and commitment, the manufacturer reports. “Assistant Q is ready to slot in to a spinning company at a senior level. He already has 65 years of Uster experience and is totally quality-minded. In addition, Assistant Q is always there, working 24/7 as part of the new Uster Tester 6,” the company explains.
Assistant Q can be observed in action at the Uster booth at ITMA Asia + CITME 2016 next month. Visitors will be introduced to him in his workplace, the Total Testing Center. Here, accurate test results are combined with real-time information from yarn clearers and additional testing instruments.
With the data from the Total Testing Center, Assistant Q has an overview of all the processes in the spinning mill. He examines test data from every production stage, alerting management to any potential issues. He directs alerts to the personnel responsible via their PCs (and in future to mobile devices) and also manages the process of solving the problem. He records when messages are acknowledged and tracks the history of the issue to its resolution.
Assistant Q also handles the routine saving valuable time for quality managers. His systematic approach aims to drive timely problem-solving and make a vital contribution to avoiding quality complaints and claims from customers, according to the manufacturer.
This new staff member takes in all the test results and provides fast analysis and interpretation. For example, he might identify changes at the carding process leading to a lower nep removal efficiency. In that case, he would immediately report the issue to the relevant operator.
The virtual assistant supports to prevent against negative feedback from buyers about unsatisfactory yarn quality for weaving and knitting applications. He evaluates fabric appearance, using a series of parameters and a grading system of 1 to 5. Yarns graded 5 are expected to be top of their class in fabric appearance. “His vast application knowledge and years of sample testing underpin this grading system,” says the company.
He is also designed to make reliable predictions for knitted fabrics, where pilling is one of the key issues. His grading here is based on the new hairiness values provided by the Uster Tester 6, as well as other parameters affecting pilling resistance.
Business intelligence for the fibre, textiles and apparel industries: technologies, innovations, markets, investments, trade policy, sourcing, strategy...
Find out more