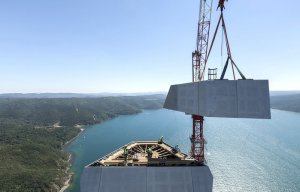
Techtextil addresses architects, construction engineers and planners
By GROZ-BECKERT KG For more than 150 years, Groz-Beckert has supported the world's textile machinery builders developing from being simply a manufacturer of knitting machine parts into the most important system supplier of precision components in the field of textiles and beyond. Step by step, the company has branched out into the business sectors of sewing machine parts, felting and structuring needles, gauge parts
1st July 2011
Innovation in Textiles
|
Albstadt-Lautingen
For more than 150 years, Groz-Beckert has supported the world's textile machinery builders developing from being simply a manufacturer of knitting machine parts into the most important system supplier of precision components in the field of textiles and beyond.
Step by step, the company has branched out into the business sectors of sewing machine parts, felting and structuring needles, gauge parts for tufting, weaving machine parts, weaving preparation parts and knitting cylinders. With the production of Ceramic Punching Components (CPC), Groz-Beckert has also in recent years become a supplier to the computer and telecommunications industry.
Groz-Beckert says it is ready to meet any challenge related to tools for the textile industry, today, tomorrow and in the future. Here, the leading German tells us about a very different challenge the company recently undertook.
At the start of the new millennium, and after only 30 years of use, the concrete girder bridge in the town of Albstadt-Lautlingen in Germany's Baden-Württemberg region, was increasingly becoming a safety risk. There was unsightly spalling and dangerous cracks in the concrete - aggressive environmental influences and corrosion had left clear traces. To guarantee pedestrians and cyclists safe passage in the future over federal highway 463 between the Stauffenberg Schloss and the school grounds, a new solution had to be found.
The requirements placed on the town as the client were clearly defined: the new bridge construction had to be given a slender superstructure, it had to fulfil increased demands regarding freeze-thaw cycles and it had to have a guaranteed service life of 80 years. On this basis, Groz-Beckert gradually had the idea of finding textile reinforcement for a new bridge, with itself as the overall project partner - and with the advantage that textiles are absolutely corrosion-resistant.
The decision to have the old concrete girder bridge demolished was finally made by the town council in July 2006. Groz-Beckert then immediately commissioned a feasibility study for a reinforced-textile-concrete bridge from the Rheinisch-Westfälische Technische Hochschule Aachen, or RWTH for short. In March 2007 the study was ready, and the prognosis was thoroughly positive regarding the material properties to be expected and the potential length of use.
The town of Albstadt also actively drove the project onward. The old bridge, beyond repair, was successfully demolished one month later.
The next important milestone came in March 2008. The town of Albstadt and Groz-Beckert co-signed a contract for implementation of the project, stipulating that the Town of Albstadt only had to pay the costs that would normally have arisen from a conventional concrete-girder design: 600,000 Euros. The additional costs of over one million Euros would be borne by Groz-Beckert.
Construction officially began for the foundations and subsequent work in November 2009. Before that, however, numerous approval processes and individual authorizations had to be organised.
The reason: As a construction material, textile concrete has not yet been regulated by standards because of its degree of innovation. Nevertheless, the construction work proceeded largely as planned. In May 2010 the prefabricated textile concrete sections were successfully mounted - and the so-called "Brückenschlag" celebration followed on May 27.
On November 5, 2010 Groz-Beckert officially handed over the textile-concrete bridge (which had already been released and approved for the start of the school) to the Town of Albstadt.
Endless rovings made from alkali-resistant (AR) glass were attached to a lattice that is a network-like structure, with axial distances of max. 15 mm. After an impregnation process during which the rovings were coated with epoxy resin, a robust reinforcement structure was created.
This remained stable in shape throughout the concreting process. Furthermore, after the impregnation process, formed reinforcement elements needed for the webs and trusses could be created.
Moreover the epoxy resin enables almost all the filaments of a roving to participate in the load transfer - resulting in the achievement of filament tensile strength.
The rovings with a diameter of roughly 2 mm thus attain tensile stresses of around 1,000 N/mm2.
Since the textile concrete bridge in Albstadt-Lautlingen is directly accessible, a practice-proven fine concrete formula was developed. It fulfils high requirements regarding frost resistance, abrasion resistance, surface quality and workability.
Because of the closely-knit textile reinforcement - with a loop width of 15 mm - the diameter of the largest grain of the surfaces was limited to 4 mm, thus successfully eliminating a screening action as far as possible. The fine concrete that was used also made it possible to create a sharp-edged cross-section geometry with a homogeneous surface.
With a length of approximately 100 metres, the textile-concrete bridge in Albstadt-Lautlingen is currently the largest of its type - anywhere in the world! Six prefabricated sections, each with a maximum length of 17.2 metres and a superstructure height of just 43.5 metres. In cross-section, the superstructure comprises a prestressed seven-web tee-beam.
The combination of textiles as reinforcement material and mono-strands for prestressing resulted in an ideal slenderness ratio. The height to-length ratio is 1:35. As a result of the articulated cross-section, formed reinforcing elements were used for the webs and trusses. The textile web reinforcement was used strategically to reduce the transversal forces. Because of the minimal concrete cover of 1.5 centimetres, the webs could be applied at the thinnest section, which is only 12 centimetres wide. The cantilever arm at the edges of the bridge narrowed down to just 9 centimetres. The use of fine concrete also made it possible to create a sharp cross-sectional geometry with a homogenous surface.
Pedestrian access to the bridge is direct - that is without an additional surface layer. The bridge is subdivided into four central areas and two end areas. Drainage takes place via defined drains in the bridge joints. The parapet is made from galvanised steel with stainless-steel mesh, and the handrail has an integrated LED strip to illuminate the upper side of the bridge. The bridge can thus be illuminated by means of spotlights from below. Their lenses can also be exchanged, enabling the creation of all kinds of different colour and light effects - to add atmosphere to events, for instance.
Although scarcely any comparable objects exist where a textile-concrete bridge is concerned, the analyses at the Institutes for Solid Construction and Building Research at the RWTH Aachen certainly give cause for optimism. They have proved that the textile structural components in the serviceability limit state are sufficient for load-bearing capacity. It was also established that the compound material textile-concrete has noticeable advantages over conventional materials where serviceability is concerned. This brings us back to the starting-point of the entire project: textiles are always rust-free!
Fully convinced of the properties of textile reinforcement, Groz-Beckert is thus assuming an extended warranty for the textile reinforced bridge of nine years. Should the bridge no longer be usable in 15 years' time, the company will finance its complete refurbishment in full. This is official proof of how much faith the company has in the bridge.
Furthermore, the slender, filigree design was only made possible in the first place by the textile-reinforced concrete. While a comparable concrete girder bridge would weigh 400 tonnes, the textile concrete bridge in Albstadt-Lautlingen weighs roughly half that amount.
With regard to sustainability - something that has always been of the utmost importance to Groz-Beckert - the textile concrete bridge in Albstadt-Lautlingen also has several benefits. The longer service life and reduction in use of materials in relation to concrete girder bridges mean that a significantly better eco-balance can be expected. At the request of Groz-Beckert, substantiated studies are currently being carried out by the RWTH Aachen in order to create absolute transparency.
With this outstanding project, the textile concrete bridge, Groz-Beckert wants to prove what today's textile technology is capable of. Technical textiles are becoming increasingly important for Groz-Beckert, its customers and partners. The spectrum ranges from applications in medical technology, automotive and aerospace engineering to architecture and construction textiles. It is precisely here that the textile-concrete bridge is creating visible and tangible proof of the possibilities.
For the town of Albstadt and especially the suburb of Lautlingen, too, this construction project is delivering entirely new and impressive visual impact. The town of Albstadt as the client, Groz-Beckert as the general contractor, and all others involved in the construction work have thus created a true landmark project - a long-term and lasting connection to the future.
Groz-Beckert KG
Parkweg 2, 72458 Albstadt, Germany
Phone: +49 7431 10-0
Fax: +49 7431 10-2777
Business intelligence for the fibre, textiles and apparel industries: technologies, innovations, markets, investments, trade policy, sourcing, strategy...
Find out more