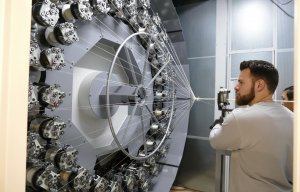
Mayer & Cie sells first 48-carrier braiding machines
Creating a unique set of material properties that balance the advantages and disadvantages of their constituent parts.
26th February 2024
Innovation in Textiles
|
Kendal, Cumbria, UK
A recent study conducted by the University of Edinburgh has highlighted the performance benefits of the 6gsm glass nonwovens developed by the UK’s Technical Fibre Products as adhesive carriers within Fibre Metal Laminates (FMLs).
FMLs combine layers of composite and metal, creating a unique set of material properties that are an effective balance of the advantages and disadvantages of their constituent parts. Initially developed for the aerospace industry, they have many advantages – they are lightweight, have a high damage tolerance and demonstrate good fatigue, corrosion and impact properties. The versatility and mechanical properties of FML technology show promise for expansion into other sectors such as wind energy and marine transport, especially when combined with new reactive thermoplastic systems.
Combining these technologies presents challenges, particularly the optimisation of the metal-composite interface for good adhesion. The constituent materials are dissimilar, potentially causing weak interfacial bonding leading to delamination and loss of integrity.
The study, Vacuum-infused thermoplastic fibre-metal laminates – Advances in bonding and recycling, evaluates the utilisation of nonwovens as a carrier for the adhesive to improve the bond line uniformity and interfacial bonding, the latter of which is characterised by a high interlaminar shear strength (ILSS). TFP’s lightweight nonwovens are already used extensively in the aerospace industry as a carrier or support for adhesive films in more traditional composite layups. They facilitate uniform wet out of adhesive, setting the bond line to ensure a defined and consistent film thickness, whilst ultimately improving the resilience and handling of the final product.
The study investigated the strength of the bonding within FMLs, evaluating the impact of using three different glass fibre carrier veils with areal weights of 6, 17 and 34gsm. The FMLs were manufactured using a standard vacuum infusion process with an adhesive carrier (fabricated using TFP’s glass veil and methacrylate adhesive) incorporated between the layers of composite and aluminium
The laminates were subjected to short beam shear (SBS) testing to evaluate the ILSS and determine which carrier delivered the most effective bonding. The results indicated that TFP’s 6gsm lightweight fine glass veil performed best – the thin, highly porous veil architecture enabled rapid and consistent impregnation with the adhesive to create a thin, uniform bond line.
The full study can be accessed here.
Business intelligence for the fibre, textiles and apparel industries: technologies, innovations, markets, investments, trade policy, sourcing, strategy...
Find out more