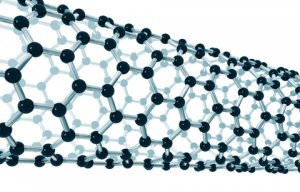
Growing uses for biocomposites
Chemically identical, sustainable alternative to carbon fibres with the same performance level.
12th June 2024
Innovation in Textiles
|
Leiden, The Netherlands
An experimental composite nose panel has been developed for the Airbus Helicopters H145 PioneerLab using bio-derived fibres based on acrylonitrile from the capture of atmospheric carbon dioxide.
The panel was flight-tested in May 2024 to demonstrate the alternative fibre’s airworthiness. As stiff and strong as the conventional part, it is small enough to produce quickly and cost-effectively and as a non-structural part, could be safely tested.
Acrylonitrile is an intermediate product usually made from crude oil, but the Airbus team used a chemically identical, sustainable alternative to produce the fibres with the same performance level. The acrylonitrile is derived from sustainable ISCC-certified non-fossil feedstocks such as wood and food waste, recycled cooking oils and algae, along with renewable sources of ammonia and propylene.
A full life cycle analysis undertaken by Airbus suggests that producing sustainable acrylonitrile and other bio-based chemicals and intermediates generates significantly less CO2 than the crude oil alternative. The industrialisation of these products, however, is in its infancy and scaling up to the extent where corresponding CO2 reductions move the dial will require regulatory commitment and massive capital investment.
For now, the PioneerLab nose panel remains a proof of concept. The challenge for Airbus and other manufacturers is to work with supply chains to make bio-fibre production economically viable, and to ensure it can be ramped up cost effectively to meet accelerating aircraft production.
Business intelligence for the fibre, textiles and apparel industries: technologies, innovations, markets, investments, trade policy, sourcing, strategy...
Find out more