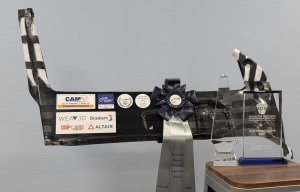
More awards for Rebar for Plastics
Door component manufactured from a topology-optimised WEAV3D structure.
13th August 2024
Innovation in Textiles
|
Norcross, GA, USA
Braskem, WEAV3D and the Clemson Composites Center at Clemson University have claimed the 2024 Altair Enlighten Future of Lightweighting Award for their development of new lightweight structural composite automotive parts.
The development project has already been recognised this year as a winner in the JEC World 2024 Innovation Awards.
The parts combine WEAV3D composite lattice woven reinforcements with Braskem’s polypropylene and are less expensive than conventional organosheets, unlocking new opportunities for the cost-effective replacement of sheet metal structures with thermoplastics throughout a vehicle.
In a proof-of-concept project, a door component was manufactured from a topology-optimised WEAV3D composite lattice comprising glass and carbon-fibre reinforced polypropylene UD tapes that were laminated to Braskem’s extruded polypropylene sheet via a continuous double belt press. The part was then thermocompression moulded in a matched-metal tool at the Clemson Composites Center and finally trimmed to dimension via a five-axis waterjet.
In flat panel testing, the WEAV3D lattice reinforced design exhibited superior load capacity and bending stiffness compared to 20-gauge stainless steel, while achieving a 65% reduction in weight. Furthermore, the lattice reinforced plastic panels were able to both absorb more energy than steel and rebound back to their original shape following large deformations, while the steel remained permanently deformed. This translates to enhanced passenger safety as the door structure can recover from deformations that would otherwise trap a passenger in the vehicle.
“This partnership has combined to create a truly innovative material that provides for a more sustainable lightweight solution to help reduce vehicle carbon emissions while enhancing the manufacturing process value through material cost savings,” says Joel Carr, technical service and development engineering team leader at Braskem America.
“Using the right material in the right place keeps costs and waste low, while still delivering substantial weight savings and performance benefits to our automotive customers,” adds Christopher Oberste, president and chief engineer at WEAV3D. “This award validates the technical development and commercialisation progress we have achieved over the past few years and recognises the importance of WEAV3D’s cost-effective lightweighting technology as part of the future of sustainable mobility.”
Using WEAV3D’s Rebar for Plastics and Braskem polypropylene reduces sheet blank weight by around 50% and final part weight by around 23% compared to conventional composite organosheets. It also increases sheet yield to 45% by weight, resulting in a 62% reduction in trim waste. Overall costs can be halved by this production route.
Business intelligence for the fibre, textiles and apparel industries: technologies, innovations, markets, investments, trade policy, sourcing, strategy...
Find out more