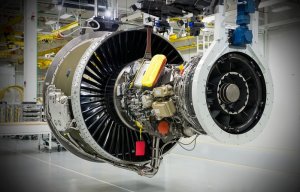
GKN Aerospace expands contract with Pratt & Whitney
The new plant will have international aerospace giants Airbus and Boeing as clients, and is scheduled to be officially commissioned next month.
8th March 2018
Innovation in Textiles
|
Tbilisi
Georgian ATC Aero, a joint venture between the Georgian Partnership Fund and Israeli weapons producer Elbit Cyclone, is finalising preparations for the unveiling of a large-scale US$85 million composites production plant in the Georgian capital near Tbilisi International Airport.
The new plant will specialize in the production of composites for the global aircraft manufacturing industry, will have international giants Airbus and Boeing as clients, and is scheduled to be officially commissioned next month.
According to David Saganalidze, Executive Director of the Georgian Partnership Fund, ATC Aero will initially produce composite parts for civilian aircraft, with its product range including aerodynamic surfaces, doors and wing parts. Almost 100% of the plant’s output will be exported. During stage two of the project, the plant will commence production of composites for fighter jets and other military aircraft. Initially, 300 jobs will be created, rising to 500 over the next few years. Planned production volumes have not been disclosed by ATC Aero, but these will be announced later this year.
According to sources at ATC Aero, manufacture will involve the use of a special technologies, that will allow the production of composites which are characterized by higher strength and provide an opportunity to the global aircraft-building industry to speed its efforts in the design of ultra-lightweight airliners and satellites. In addition to higher strength, the composite materials will be able to withstand a temperature range of 300-350°C.
Mikhail Pogosyan, a former general director of the United Aircraft Corporation (UAC), a Russian aircraft manufacturer, said the use of composites in aircraft-building is not as wide as is presented by some analysts.
“The use of composite materials in the fuselage gives a noticeable gain in weight, but only for wide-bodied aircrafts. Studies conducted in the UAC showed the gain in mass becomes noticeable only for fuselages wider than 6 m. Therefore, the use of composite materials gives the greatest benefit in the wing: in addition to weight reduction, their improved strength characteristics allow for a greater elongation of the wing, which significantly improves the aerodynamic characteristics of the airframe and directly affects fuel consumption. According to various estimates, this factor saves 6-7% of fuel,” Mr. Pogosyan commented.
“Today, only Boeing 787 Dreamliner has the wing, which is entirely composed of composite materials, however, there is a possibility such a situation will change already in the coming years.”
According to analysts at the Russian Ministry of Transport, the consumption of composites by the global aircraft-building industry will continue to grow in the coming years, as the use of composites makes it possible to produce large elements of the airframe, reducing labour intensity and costs by reducing riveting and joints.
Business intelligence for the fibre, textiles and apparel industries: technologies, innovations, markets, investments, trade policy, sourcing, strategy...
Find out more