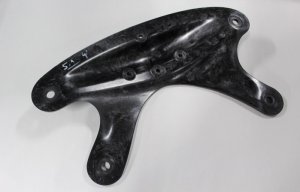
High-volume, zero-waste process with Hexcel moulding compound
Unlocking the commercial viability of desirable products which currently have no cost-effective manufacturing method.
2nd July 2024
Innovation in Textiles
|
Sheffield, United Kingdom
PolyMorphic moulding is a technology developed by Sheffield, UK-based Fyous with infinite possibilities for manufacturing products such as parts based on combinations of carbon fibre composites and PU foams, in addition to customised multi-component footwear.
The technology can shapeshift in under 20 minutes, producing zero tooling waste and making usable parts many times faster than 3D printing.
It features more than 28,000 densely-packed pins that create the mould. Once the pins are in position, the mould can withstand six tons of distributed pressure.
As such, patent-pending PolyMorphic moulding has the potential to transform the manufacturing industry, reducing the waste generated through tooling amends, coupled with the faster production times compared to 3D printing and traditional mould-making.
By inputting a 3D CAD model, Fyous software generates the mould shape and the company’s machine then shapeshifts the mould to create the specified product.
On completion of a project, the PolyMorphic mould is returned to the machine, ready for its next configuration. The system is suitable for any process typically based on moulds, including vacuum forming, foam casting, food production or composite layup.
Zero tooling
One product example is a bike saddle made from carbon fibre and PU that would conventionally require two moulds and associated tooling that once used, would either need storing or be wasted.
PolyMorphic moulding enables both parts to be rapidly produced from the same piece of tooling with zero tooling waste.
In this case, Fyous made both mould and tooling in just 60 minutes. The foam was cast, and the carbon was laid up and left to cure for three hours under a vacuum at 60 degrees and then left for another 12 hours. The process removes the cost of tooling for making such parts with a 24-hour turnaround and very little labour.
PolyMorphic moulding also enables advanced opportunities for customisation and in addition to footwear components, has been used to produce custom-fit protective face masks for sports, which are costly, primarily due to the intricacies involved in 3D printing them.
Fyous ran a case study to make a lightweight carbon fibre protective face mask using its mobile scanning app and PolyMorphic moulding. 3D scanning can now be done at home using Apple’s iPhone and the Fyous 3D scanning app, taking just minutes. Using PolyMorphic moulding, Fyous was able to create a custom mask mould in under 20 minutes to significantly lower the cost of customised carbon fibre parts.
“Using PolyMorphic moulding to rapidly create accurate moulds for tooling will reduce time to market for a huge array of products and unlock commercial viability for desirable products which currently have no cost-effective manufacturing method,” says Joshua Shires, co-founder of Fyous “Our mission is to deliver this disruption whilst reducing environmental impact. PolyMorphic moulding is a zero-waste technology where raw materials are conserved and the moulds can be used again and again. We will remove not only physical waste in the form of materials and tooling, but also remove wasted time by accelerating product development, prototyping and manufacture efficiencies.”
Business intelligence for the fibre, textiles and apparel industries: technologies, innovations, markets, investments, trade policy, sourcing, strategy...
Find out more