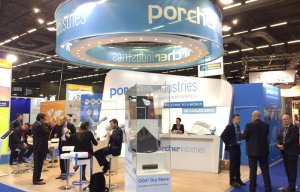
Enabling high speed production with Dry Fiber
Electroimpact, of Mukilteo, Washington, has increased the laydown speeds for thermoplastic unidirectional tapes to over a hundred metres (4,000 inches) per minute.
13th January 2021
Innovation in Textiles
|
Thornton Cleveleys, UK
Using its enhanced automated fibre placement (AFP) processing technology, US provider of factory automation and tooling solutions Electroimpact, of Mukilteo, Washington, has increased the laydown speeds for thermoplastic unidirectional tapes to over a hundred metres (4,000 inches) per minute, using a new material made by Victrex, of Thornton Cleveleys, UK
Currently, large composite structures in aerospace such as wings, and fuselage are virtually all thermoset based and require a lengthy cure in an autoclave large enough for the structure.
The autoclave is a production bottleneck and uses a considerable amount of energy. OEMs and their suppliers are not only looking to improve the fuel efficiency of aircraft but also efficiencies along the supply chain. The substantial benefit thermoplastic composites offer has been investigated for some time, and this has led to its increasing adoption for the manufacture of smaller parts. Thermoplastic composites can be processed out of autoclave so manufacturing processes have been developed to take advantage of their potential for high-speed production. The recyclability of thermoplastic composites is another major advantage as well.
“The significance of processing thermoplastic UDT at 4,000 inches per minute layup speeds with the variable spot size (VSS) laser is, for the first time that we know of, that thermoplastics are able to achieve thermoset layup speeds,” said Michael Assadi, chief engineer at Electroimpact. “These developments can help eliminate the need for autoclave cure, offer major and new, throughput advantages for thermoplastics,” explains.
Electroimpact have enhanced existing AFP processing technology through the deployment of a new laser heating system with the potential to revolutionize thermal processing for the aerospace industry.
“We are really excited to offer this new laser technology and using the high-performing low melt PAEK composite material from Victrex on a broader scale to meet unmet customer needs. I’m convinced, that based on ongoing in-depth support from Victrex at every stage of the project, high speed production and high performance of the advanced Victrex AE 250 UDT will enable the production of large-scale aerospace structural components in the years to come.”
A test program comparing several different materials demonstrated, that the Victrex LMPAEK UDT delivered the best performance in producing porosity-free laminations, including the most dimensionally uniform and even distribution of fibre in the resin. As a result, a high quality component can be produced without any additional processing steps after layup, eliminating the need for oven consolidation.
Victrex AE 250 LMPAEK UDT was designed by Victrex to have mechanical, physical and chemical resistance properties typical of the PAEK polymer family, but with a 40°C lower crystalline melting temperature of just 305°C.
Business intelligence for the fibre, textiles and apparel industries: technologies, innovations, markets, investments, trade policy, sourcing, strategy...
Find out more