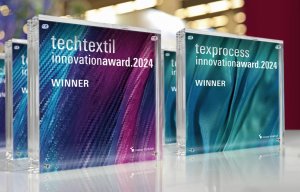
Changing the world with textile innovations
Opinion
Marie O’Mahony reviews some of the outstanding innovations which were presented at this year’s Frankfurt show.
11th June 2024
Marie O'Mahony
|
Frankfurt, Germany
Smart Textiles had a strong presence at Techtextil in Frankfurt this year, as developments showcased ranged from graphene to pressure sensing, thermal signature shielding, as well as efficiencies achieved in manufacturing processes such as dual system-in-package (SiP) design. Heathcoat Fabrics, Noble Biomaterials, the German Institutes for Textile and Fiber Research (DITF) and Fraunhofer IZM were amongst the innovators.
Graphene for performance apparel
Heathcoat Fabrics included a new range of fabrics that incorporated graphene. This is a collaboration with Directa Plus, who produce nanoplatelets-based products for applications that include textiles for performance apparel and workwear.
The fabrics have been developed as concepts to show the knit company’s capability in this field as it is best known for its expertise in 3D Spacer, mesh and other performance knits. Showcasing the new fabrics, it used a honeycomb pattern that serves to emphasise the structure of graphene’s carbon atoms.
The Heathcoat fabrics are lightweight and knitted in a fine gauge while carrying the unique properties of graphene, notably electrical and heat conductivity. Used in thermal regulation, the textiles can deliver advanced heat dissipation and offer an increased cooling rate of up to 60%. Additional qualities include a strong surface resistivity that makes it well suited to anti-static applications, as well as antibacterial properties.
Noble Biomaterials's Circuitex
The military has been a primary driver in smart materials for wearables from a very early stage of development, providing clearly defined performance needs and a potentially large market segment. Noble Biomaterials specialises in metalised coatings for fibre and fabric applications that include conductivity, sensing, broad-spectrum shielding, antistatic and antimicrobial protection.
The Circuitex range of yarns, fabrics, tapes, foam and wallpaper provide lightweight, flexible conductivity and EMI shielding. The applications for Circuitex includes smart wearables, Internet of Things (IOT) fabrics, pressure sensing as well as smart soft surfaces. While a number of different metals can be used including gold, silver is the most common and it is applied with a micron-thin layer of 99.9% pure metal that is permanently bonded to a stretch, or non-stretch nylon.
The fibre and fabric weights can be varied as can the level of conductivity with options as low as 0.006 Ω/square in electrical resistance. The recent development of Circuitex Sigma points to a next level of innovation for smart materials in the defence sector. It brings the added capability to reflect electrical registrations and shield a range of emissive thermal signatures including body heat, engine heat and active firearms. This affords additional protection to military personnel allowing them to remain virtually undetectable to enemy advanced sensors.
Addressing work-related musculoskeletal disorders
In North America, the Institute in Medicine estimates the economic burden of work-related musculoskeletal disorders (WMSD) as between $45 and $54 billion each year. This figure includes office workers with the trend to home and hybrid working exacerbating the problem of poor posture and prolonged sitting.
The German Institutes for Textile and Fiber Research (DITF) working with SME partner Roma-Strickstoff-Fabrik Rolf Mayer, have developed a smart office chair directed at addressing poor posture and extended occupancy that could lead to back pain. The pressure sensing technology is incorporated into the fabric of the seat and backrest, designed to be invisible and not interfere with haptic or comfort.
The data is communicated to the sitter via an app, and it could also be displayed in an illuminated armrest of the chair. The clear traffic light colour coding is intended to catch the sitter’s eye and prompt movement, exercise or a position change of the body. People working on computers as well as in leisure such as engaging in gaming activities are seen as benefiting from the technology in particular.
Fraunhofer Institute
Researchers at the Fraunhofer Institute for Reliability and Microintegration showcased a number of developments including new developments in smart patch design for the monitoring of vital signs.
As part of the Horizon 2020-funded Applause Project (Advanced packaging for photonics, optics and electronics for low-cost manufacturing in Europe ) researchers at the System on Flex group at the institute, alongside 31 consortium partners, have developed a flexible cardiac monitoring patch and miniaturised cardiac implants that have advanced monitoring capabilities. The intention being to refine the technology to ‘Plug and Play’ to the point where it becomes as thin and flexible as a regular medical plaster.
Developing a stretchable printed circuit board (SCB) using a thermoplastic polyurethane (TPU) substrate is the basis of the development. Assembly has been addressed from an early stage, with the electronic components integrated as part of a dual system-in-package (SiP) design mounted directly onto the flexible printed circuit board (PCB).
Considering the manufacturing process throughout has directed the development in a way that has helped to ensure that any issues around bringing each of the different elements together can be addressed in a more timely way throughout the project. The benefit of this reaches beyond the individual project as the principles of SiP design can be applied across the broader field of Flexible Hybrid Electronics (FHE).
Business intelligence for the fibre, textiles and apparel industries: technologies, innovations, markets, investments, trade policy, sourcing, strategy...
Find out more