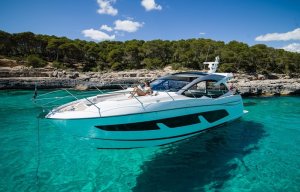
Sunseeker selects Hexcel’s HiMax DPA technology
Lightweight, nonwoven semi-preg eliminates the need to use a traditional in-mould gel coat.
26th January 2022
Innovation in Textiles
|
Stamford, CT, USA
Yacht builder Sunseeker has chosen Hexcel’s HexPly XF surface technology to produce prepreg parts with high-quality, paint-ready surfaces quickly and efficiently for its latest 90 Ocean luxury yacht.
The lightweight composite hardtop for the yacht is manufactured with a combination of HexPly XF and HexPly SuperFIT semi-preg. It is lighter in weight than versions made using resin-infusion processes, and it de-moulds with a pinhole-free surface that needs minimal preparation to be ready to paint. Sunseeker has recorded an overall reduction in process time of around 30%, saving three days of manufacturing time per hardtop.
The hardtop provides shade and protection for the yacht’s uppermost deck space. Its reduced weight helps to ensure the stability of the vessel, and the paint-ready finish provides Sunseeker with more options for customising its colour to the individual needs of its clients.
HexPly XF is a lightweight, nonwoven semi-preg that eliminates the need to use a traditional in-mould gel coat. The surface technology significantly reduces the costly and time-consuming refinishing work typically required to impart a paint-ready finish to prepreg or semi-preg parts, and yields lightweight, consistent components in short cycle times.
Working with Sunseeker, Hexcel developed a material format, a laminate ply sequence and a production process that satisfied the structural requirements for the hardtop and enabled the yacht builder’s production team to lay up and cure the part in a single shot.
Hexcel supplies Sunseeker with a HexPly XF product that comprises both the surface layer and the first structural reinforcement ply, eliminating the need for a cosmetic barrier coat. Neither the HexPly XF surface layer or the following layers of HexPly SuperFIT require debulking steps and both are based on Hexcel’s rapid-curing M79 epoxy resin system. Adhesive resin films are not needed to bond the hardtop’s foam core, as the resin content of the SuperFIT plies has been adjusted to further reduce overall process time.
Once de-moulded, the cured hardtops are inspected before they are passed to Sunseeker’s finishing and painting technicians for final preparation and painting. The HexPly XF resin surface allows the yacht builder’s quality technicians to inspect the laminate below quickly and easily, ensuring the quality and consistency of the structural reinforcement plies.
“Composite materials that improve our production processes, as well as great technical support, are what makes working with Hexcel such a success story,” said Stuart Vaughan-Jones, composite development manager at Sunseeker. “With the switch from gel coat and resin infusion to HexPly XF and SuperFIT in the new hardtops, we are now building lighter, more consistent parts, more quickly than before, with a higher quality surface finish. XF really has ticked all the boxes.”
Business intelligence for the fibre, textiles and apparel industries: technologies, innovations, markets, investments, trade policy, sourcing, strategy...
Find out more