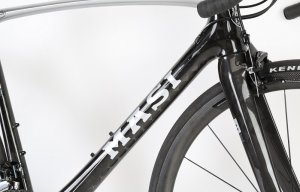
Lightweight bikes reinforced by TeXtreme
Commingled carbon fibre and nylon yields improved fibre deposition for maximum performance.
31st January 2022
Innovation in Textiles
|
Bristol, United Kingdom
The UK’s National Composites Centre (NCC) has worked with Bristol-based Starling Cycles and Composite Braiding, of Derby, to demonstrate the use of thermoplastic carbon fibre for an electric mountain bike frame which will enable it to be both repaired and recycled at end of life more easily.
Whilst composite bikes are already readily available, they are mostly made from thermoset epoxies, which, because they are resistant to heating, cannot be broken down and repurposed at end of life. To counteract this, the project team set out to develop a frame for an electric bike using thermoplastic carbon fibre.
Thermoplastics can soften when heat is applied to them and can be re-shaped which means that not only can they be repurposed if needed, but importantly, they can also be repaired throughout their use, increasing their lifespan.
The demand for E-bikes in Europe is expected to grow significantly in the coming years, with anticipated sales increasing from 3.7 million bikes in 2019 to 17 million in 20301. Currently, Starling Cycles manufactures its handmade E-bike frames from steel. By using a thermoplastic composite frame instead, the range of the bike will be increased due to the weight reduction, as well as offering a more sustainable product.
As well as conducting a life cycle assessment (LCA) of Starling Cycles’ existing manufacturing methods and the frame design, the NCC developed a novel manufacturing process to create the lugs required to hold the frame together.
Using a commingled material of carbon fibre and nylon, the new method facilitates an improved fibre deposition for maximum performance. Commingled materials combine the fibre and resin into a single material, removing the need to separately infuse the resin later in the manufacturing, making it a more efficient process.
The LCA allowed Starling Cycles to ascertain where future improvements can be made to its design and manufacturing process to make further reductions to the environmental impact of the product.
In addition to showing that thermoplastics are a strong enough material to be used for a bike frame, the expanded understanding of how they can be re-worked and re-used opens the door to using thermoplastics in other components across industry due to the flexibility they offer. They can also offer higher production rates (due to the lack of separate infusion processes), whilst still providing the high quality of composites, potentially allowing for a reduction in costs and environmental impact.
Business intelligence for the fibre, textiles and apparel industries: technologies, innovations, markets, investments, trade policy, sourcing, strategy...
Find out more