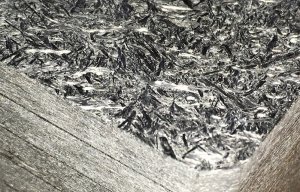
Interview with Simon Price and Tim Bastow, CFP
The manufacturer has developed the ability to commercially manufacture 3D carbon fibre preforms for composites which require no post knitting fabrication.
30th June 2017
Innovation in Textiles
|
Derby
Billy Hunter reports
A UK-based manufacturer of weft knitted technical textiles has developed the ability to commercially manufacture three-dimensional carbon fibre preforms for composites which require no post knitting fabrication or cutting and importantly produce no waste.
Derby-based Preform Technologies has just completed a two-year Knowledge Transfer Partnership (KTP) project with the University of Derby, the aim of which was to modify and adapt a Stoll CMS 822 HP v-bed weft (flat) knitting machine to retain its full functionality while knitting carbon fibre. KTPs are government-funded programmes encouraging collaboration between businesses and universities in the UK.
“We were asked so many times if we could make the preforms we were already manufacturing from glass fibre out of carbon that saying no became embarrassing,” says Preform Technologies CEO Sylvan Whalley. “This has been the ‘holy grail’ of 3D knitted composite reinforcements and we fully understood what achieving it would entail. The increasing number of enquires for carbon preforms led to an internal feasibility study, which resulted in our KTP project, which concluded at the end of last month.
“We have achieved a world first capability here, bringing the benefits of our shaped glass RTM preform expertise to that of carbon fibre – shaped parts, requiring no fabrication or cutting to fit a mould tool, and importantly reduce waste.”
It’s no surprise that Preform Technologies were swamped with enquiries for 3D carbon preforms, since demand for the material is booming. According to leading analyst Lucintel, the global carbon fibre market will grow at a CAGR of 11% by value from 2016 to 2021 and the major growth driver is the growing demand for lightweight materials in a range of end-use industries. Current global carbon fibre capacity stands at around 121,000 tonnes with predicted global demand in 2020 ranging between 240,000 and 340,000 tonnes.
“It’s been an interesting project and we are delighted with the outcome, especially since we are now able to progress from development to full production,” Whalley adds.
The KTP has allowed the company to assemble a team with the skills which it was lacking in-house and provided access to the resources of the University of Derby. It also allowed a post graduate KTP Associate, Michalis Christophides, an electrical and electronic engineering graduate, to be appointed and be completely dedicated to the project. KTPs cover different time-frames ranging from 3-24 months, but Preform Technologies chose two years as it was obvious that the task in hand would be more complex than it first appeared.
A significant aspect of the project was the construction of the clean room/machine environment which fell outside the KTP and was totally funded by the company. This was viewed as essential in providing a safe working space before the project started.
The main challenge however, related to adapting the machinery for purpose.
The latest generation of flat knitting machines have achieved a step-change in capability, primarily due to a focused attempt by the machine builders to address the needs of an emerging technical textiles sector, by improving the control and placement of yarns within knitted structures and enabling the creation of more complex fabric structures.
However, these advances do little to facilitate the manufacture of carbon fibre components. Knitting carbon fibre is not the issue – modern machines can knit carbon fibre tapes, tows, spun yarns and more – the problem is that the carbon fibre itself is electrically conductive.
Issues related to the conductive nature of the fibre compromising the abundant sensitive electronic components have prevented progress in this direction. Items such as power supplies, motors, solenoids, on-board computers and PCBs, touch screen interfaces and USB data transfer ports are all extremely vulnerable.
“Achieving our aims is significant, given that the machine is loaded with vulnerable electronics, with two computers on board, various motors, yarn carrier selector solenoids, open circuit boards, and other sensitive equipment all of which are at significant risk,” Whalley says.
When processing carbon fibre via technologies such as weaving, multiaxial warp knitting, braiding and others, the problem of protecting vulnerable electronics is overcome by separating the electronics and motors which control and drive the machine, from the machine itself. This is often done by housing them in different rooms and connecting via cables.
In the case of electronically controlled flat knitting machines, this presents a bit of a challenge as it is not practical to introduce cables longer than a few metres without essential signaling being interrupted. The solution lies in introducing numerous complex measures to protect motors, circuit boards and other components, which is largely what the Preform Technologies KTP was about.
Preform Technologies has taken an innovative approach, drawing on its expertise in V-Bed knitting technology and fabric engineering. The development of performance textiles and substrate materials is driven by the requirement to provide lighter weight, stronger and more efficient materials in both rigid and flexible forms, increasing the already demanding specification of the finished product.
“The challenge to deliver both performance and efficient manufacturing is one that our knitted fabrics and 3D performs can achieve by providing pre-formed or shaped articles ready for use in application, either to be loaded directly into an injection mould or as part of a component assembly, reducing the need to fabricate or significantly tailor to fit, increasing efficiency by reducing handling time and waste,” Whalley says. “Our preforms service a broad range of industrial sectors, and deliver net-shape reinforcements which simplify tool loading by eliminating the cutting and fabricating of conventional substrate materials such as woven or multi-axial fabrics, saving time and money and eliminating waste. Continued investment in the latest technology and state of the art v-bed knitting machines maintains our leading position at the cutting edge of product development in new and existing markets.
“Our recently-developed ability to manufacture carbon fibre preforms, opens the door to new horizons for automotive, aerospace and marine applications, introducing our knitted fabrics, and preforms to manufacturers of carbon fibre reinforced products,” he adds. “We can now offer what we believe to be a world first for flat knitting, producing shaped carbon fibre preforms in volume.”
Many Preform Technologies customers often request a quick indication of the production cost and end use functionality of their product – in other words, they want fast answers to the questions of ‘will it work?’ and ‘how much will it cost?’ In addition, during a development process, time versus cost constraints can typically limit the effort given to evaluating the merits of numerous possibilities.
“This is where quick and informed decisions save time and money, and although the products of two customers are hardly ever alike, we understand the manufacturing process and derive the benefits of the low cost set up that our technology can offer,” Whalley says. Regarding our carbon preform capability “As we move from development into a productive capacity, our focus is turning to commercialisation, and we are seeking opportunities to work with customers to supply weft knitted fabrics and preforms in carbon.
It’s been very interesting, occasionally frustrating, but overall an enjoyable experience, and we are delighted with the outcome.”
Husband and wife team, Sylvan and Cynthia Whalley established the family business in 1995 and with a strong heritage of technical knitting applied to Industrial applications, Preform Technologies are manufacturers of weft knitted fabrics and shaped preforms. The company’s expertise in fabric engineering and ability to process a diverse range of fibre types, coupled with the ‘low cost’ set up of flat knitting technology enables it to provide cost effective solutions to problems encountered by designers, engineers, and technologists.
The company is quality accredited to ISO 9001:2015.
Further Information
Preform Technologies Limited
Centurion Way, Business Park
Alfreton Road
Derby
United Kingdom
DE21 4AY
Contact: Sylvan Whalley
Email: [email protected]
Tel: +44 (0)1332 366587
Business intelligence for the fibre, textiles and apparel industries: technologies, innovations, markets, investments, trade policy, sourcing, strategy...
Find out more