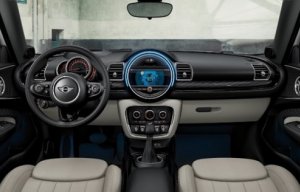
Sabic reduces weight in instrument panel carrier
According to North Carolina based Precision Fabrics Group (PFG), its’ commercially successful Nexus AFR approach is a new paradigm for sound absorbing car parts design. Based on acoustical physics/science principles, the development work to create the new facing product was only one of the significant hurdles that this new idea had to clear to achieve commercial success. The concept, the company says, had to be explained to non-technical individuals in a way that they could understand and it had to be validated with measured performance data to achieve commercial status.
17th December 2013
Innovation in Textiles
|
Greensboro, NC
According to North Carolina based Precision Fabrics Group (PFG), its’ commercially successful Nexus AFR approach is a new paradigm for sound absorbing car parts design. Based on acoustical physics/science principles, the development work to create the new facing product was only one of the significant hurdles that this new idea had to clear to achieve commercial success. The concept, the company says, had to be explained to non-technical individuals in a way that they could understand and it had to be validated with measured performance data to achieve commercial status.
“Every new technical proposal reaches the stage where it has to be explained to the user. The user or purchaser has to have confidence that “it will work” and “it is worth it”. In this situation the task involved convincing a sceptical audience that all of their historical experience was “not optimum”, and that all of the “rules of thumb” they have used in acoustics may not apply. All this occurred in a situation where the deliverable was basically invisible,” says PFG’s Rich Bliton.
Existing Rules of Thumb or Sacred Cows |
New paradigm
|
Heavier fibre layer provides better acoustic performance |
Loft layer thickness is important – but density can be reduced for cost and weight savings
|
The scrim (facing) fabric is non-acoustic |
The facing can provide significant acoustical contribution |
A way to reduce weight is to use lighter scrims |
Slightly heavier AFR facings can lead to significantly lighter overall composite weight
|
The price of all materials had to be reduced to reduce the total part cost |
Higher price AFR facings can lead to lower total price parts
|
According to Bliton, the method typically used to evaluate acoustical performance is to make a sample part and put that part in a special reverb room. A series of calibrated sounds are then broadcast through special speakers, and the decay of sound is collected via special microphones. This process is first performed with the room empty, and then with the sample in the room. The data from the first run without the sample is then subtracted from the case with the sample in the room. The difference between these measurements is then the sound absorption of the test sample alone.
This process, Bliton says, provides good data and has been the conventional basis for development of new materials and parts and also is the established yardstick for qualification. The data is usually presented in a graphical manner that non-acousticians can easily understand - higher is always better, Bliton adds.
The disadvantage of the conventional method, Bliton says, is that a sample must be fabricated to be evaluated and the time line to conceive a multi-layer material, order materials, produce prototype samples, ship to the test facility, perform the test and receive the data is long and expensive. According to Bliton, a single iteration could in fact take 6-8 weeks with test costs of over $2500 for a typical set of samples in a full size reverb room. A development project could easily cost $25,000 and take 6 months, Bliton explains.
The path to launch for a product like the Nexus AFR for example could have required multiple iterations of samples and data reviews to be accepted and tens of thousands of dollars and many months may have been required.
However, PFG and acoustical consultant, Michael Dinsmore (Acoustical Consulting Services), discussed the situation and agreed to implement a virtual approach to designing, evaluating and accurately predicting performance data for acoustical absorption parts.
“It turns out that advanced acoustical modelling software has been commercially available for a number of years. Software packages have been fully validated and accepted by experts in the global acoustical community, but not widely used due to their complexity,” Bliton says.
The modelling approach selected was the Biot Theory combined with the Transfer Matrix Method and according to PFG the approach defines multiple modelling parameters for each solid, perforated or porous material layer type, or fluid, such as air, which constitute each multi-layer composite.
“Some of these parameters are very difficult to measure directly. This has limited the usefulness of this modelling approach outside the theoretical community. Mr. Dinsmore has taken advantage of a practical approach to inversely define the more difficult modelling parameters,” Bliton explains.
“Acousticians have a lab test device called an Impedance Tube. This device is used to measure the acoustic properties of a material when the sound is limited to 00 or perpendicular angle of incidence... the device is small, relatively inexpensive and readily available. The problem with the test data is that it is limited to perpendicular or normal incidence only. This test data does not match up with the reverb room random incidence (0-900) data the industry typically uses to evaluate performance,” Rich Bliton explains.
Dinsmore’s approach uses the measured normal performance from the impedance tube to inversely determine the more difficult parameters in the acoustical modelling approach.
“Once all modelling parameters of each layer have been determined, multi-layer models became “practical” for use. Using this virtual approach, multiple scenarios with various thickness, fibre densities, facings or scrims can be evaluated and compared side-by-side in reverb room or random incidence data format,” Bliton says.
Once the set of modelling parameters has been established for each layer of a particular composite construction, Dinsmore then uses the sophisticated modelling software to simulate full size reverb room tests of finite-size, multi-layer composite test samples.
This, Bliton says, provides the way to explain the PFG alternative approach that uses a slightly heavier, more expensive AFR material and yet reduces overall weight, improves acoustics and reduces overall cost. PFG says it has used the modelling to create side by side comparisons of conventional versus alternative composite designs with reliable modelling data that the reviewers could identify and validate to in house data.
The most significant aspect of this approach was that the data could be created within days at a very low cost. Rich Bliton explains that the process of convincing the non-acoustician with side-by-side data in a format that was familiar is much more direct than trying to explain complex acoustical principles. The flexibility of the modelling to generate exact scenarios for various thickness and densities helps to draw the potential end-users into the discussion, he adds.
“The speed of the feedback from idea to results increased the momentum. Psychologists say that this is the same reason that kids get addicted to video games. The instant gratification from seeing the results of their actions is very rewarding,” Bliton enthuses.
Once the approach has been accepted, the team uses the model to accelerate the development process and products are evaluated virtually once various design candidates are brainstormed, the results then helping to narrow down the top candidate designs. Often only one or two samples are made and tested to verify the results of the modelling.
Bliton goes on to explain that having accurately predicted acoustical performance data available at the beginning of the discussion with various OEMs changes the discussion. The meeting evolves from reacting to an RFQ with many questions to proactively proposing new customer values for weight reduction, performance improvement and/or cost savings based on reliable modelling data.
Applying proven acoustical modelling approaches to shorten the development cycle reduce part weight and possibly save money is an example of how physics can be used to reduce weight in cars.
Using the Physics of Acoustics to Reduce Weight in Cars
Precision Fabrics Group
301 N. Elm St, Suite 600, Greensboro, NC 27401, USA
Tel. 001 800 284 8071(office)
Business intelligence for the fibre, textiles and apparel industries: technologies, innovations, markets, investments, trade policy, sourcing, strategy...
Find out more