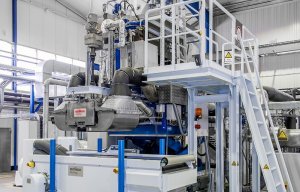
Oerlikon Nonwoven closes a deal at IDEA
The plant has now been running for several weeks under stable production conditions with optimal nonwoven fabric quality.
5th February 2021
Innovation in Textiles
|
Neumünster, Germany
Oerlikon Nonwoven has successfully commissioned a double beam meltblown plant with ecuTEC+ electro charging unit at Wolf PVG GmbH & Co. KG. With this plant, the East Westphalian company can now provide nonwovens for the production of surgical and FFP2 masks. In addition to the filter material, which is in great demand, high-quality meltblown nonwovens can also be produced for medical and industrial filter applications. The plant has now been running for several weeks under stable production conditions with optimal nonwoven fabric quality of the highest standards, Oerlikon reports.
At the beginning of the corona pandemic and the shortage of protective masks that ensued, Wolf PVG GmbH & Co. KG, a wholly-owned subsidiary of the Melitta Group, switched part of its production capacities to nonwoven mask fabric production. As a highly specialised system supplier for everything to do with vacuum cleaners and industrial filter technology, the company can fall back on its extensive know-how and many years of experience, says Oerlikon.
With the meltblown plant from Oerlikon Nonwoven, Wolf PVG is further expanding its production capacities. The plant, with its two beams and the ecuTEC+ electro charging unit, is optimally designed for the production of face mask material, the company explains. The plant is also ideal for the production of other filtration nonwovens.
“A decisive point for investing in a plant from Oerlikon Nonwoven was the flexibility of the plant in relation to the possible product portfolio and the competence of the manufacturer,” explains Markus Seele, COO of Wolf PVG.
Dr. Ingo Mählmann, Senior Vice President Sales & Marketing Oerlikon Nonwoven, adds: "Thanks to the numerous setting options for the electrostatic charge provided by the ecuTEC+, the optimum loading status can be set depending on the filter application."
Oerlikon Nonwoven’s meltblown technology is considered the most technically efficient process for the production of highly effective filter media from plastic fibres. The ecuTEC+ electro charging unit also makes a significant contribution to this. With the patented process, spunbond and meltblown materials can be charged electrostatically and thus the filter performance can be significantly increased. In this way even the smallest particles are safely filtered. Nonwoven manufacturers are thereby largely free to choose and can set the optimal charging method and intensity for their filter application, concludes Oerlikon Nonwoven.
Business intelligence for the fibre, textiles and apparel industries: technologies, innovations, markets, investments, trade policy, sourcing, strategy...
Find out more