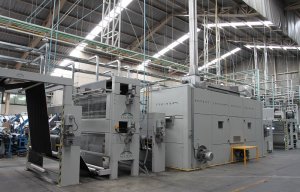
Mexico’s Tavemex reduces water usage by 80% with Monforts Eco Denim Line
TCE, Vietnam’s biggest denim producer, celebrates the first year of its Eco Line installation achieving close fabric control and significant energy savings benefits.
19th October 2017
Innovation in Textiles
|
Vietnam
TCE, Vietnam’s biggest denim producer, celebrates the first year of its Eco Line installation achieving close fabric control and significant energy savings benefits.
TCE Corporation was the world’s first denim producer to install a Monforts Eco Denim Line, and after a full year of production is now able to evaluate the advantages in terms of production and energy and water savings.
The company is the largest producer of denim in Vietnam, and one of the largest in Asia.
Founded in South Korea in 1956, TCE relocated its entire production to Vietnam in 2014, and now produces only denim at its TCE Vina Denim mill, which occupies a 110,000m² site two hours outside of Hanoi.
TCE exports 100% of its production overseas, with Europe, at about 45% being the largest market, followed by the USA at 30%, and Japan and Korea the other main export destinations.
Chief executive officer Stanley Hwang says that production ranges from lightweight to heavyweight denim, in the range of 4 to 14 ounces.
“The critical point with denim is consistency and shrinkage,” he says. “The greatest benefit of the Eco Line is that it allows the fine control of fabric shrinkage.
“We are a long-time user of Monforts, having installed our first machine in 1996, a machine that is still in full operation.
“We then progressed to the second-generation machines, where we can control the shrinkage but it can be complicated.
“With the Eco Line, we can see exactly what is going on in the production line, and it is very easy to operate. We have complete control of the shrinkage, and we need one or two less staff to operate the machine.”
The Eco Line was manufactured by Monforts in Germany and supplied via Peja Vietnam, Monforts representative for Vietnam.
The Eco Line is engineered to save on water and energy usage.
At the front of the machine is the Eco Applicator which applies the chemicals, replacing a conventional padder and applying less moisture to the fabric, reducing drying needs and therefore energy consumption.
After this stage, the Thermex Hotflue Chamber generates the necessary moisture and temperature for making the denim stretchable, whilst incorporating a soft stretching of the fabric using many rollers instead of only the one or two used in a traditional stretching unit.
This consequently saves on the volume of water needed to generate the steam, and also saves on the amount of energy required to convert the water to steam.
Mr Hwang says that TCE is saving on both water and electricity. Water is taken from the public supply, for better quality and convenience than a well, and savings are in the region of 20 to 30%. Electricity savings are around 10%.
TCE had started to make denim in Korea in 1969, and was probably the third Asian producer to do so.
“We were the first denim producer in Korea to use Monforts machines,” says Mr Hwang.
“Monforts for us is very safe. So although other companies approached us when we were planning to expand production, there was no doubt on our part that we would install a new Monforts machine.
“The consistency we achieve with Monforts is perfect. We love Monforts!”
Production general manager Ku Myung Soo says that the fabric passes in one continuous run, through the Eco Applicator, then through the Thermex, and finally through the shrinkage process.
“There are three main stages,” he says, “and the fine-control system allows us to closely monitor the entire process.
“Monforts sent an engineer from Germany to install the machine and train the staff, and we have continual backup from the Peja team, with who we work closely.
“Our production staff find the Eco Line very easy indeed to work with.”
Investment in the Eco Line came as part of an important expansion to coincide with TCE’s 60th anniversary last year, and which boosted output from 1.5 million yards a month to 3.5 million yards, the biggest production capacity in Vietnam. The Eco Line throughput is 1.5 million yards.
There is anticipation that the demand for Vietnam denim will increase substantially when the European Union Free Trade Agreement with the country comes into effect, which is expected to be at the beginning of 2018.
TCE is additionally implementing its own vertically integrated facility including garment manufacturing to provide a full package for buyers.
Mr Ku explains that the company produces its own rope dyeing machines, the entire design, manufacturing and installation of the machines being carried out by the TCE team.
There are now five rope-dyeing machines to cope with the new production capacity, the latest having 22 dips to provide the dark indigo colour that is demanded by certain sectors of the market.
TCE has a total workforce of around 1,800, and works 24 hours a day, usually six days per week but seven when necessary.
Business intelligence for the fibre, textiles and apparel industries: technologies, innovations, markets, investments, trade policy, sourcing, strategy...
Find out more