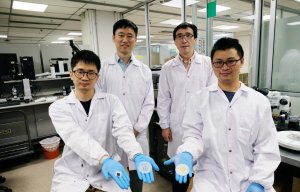
Biodegradable printed paper power
Device incorporates a “Li-Fi” communications system in which pulses of light are used to transmit data.
30th December 2021
Innovation in Textiles
|
Cambridge, MA, USA
MIT researchers have developed a rechargeable lithium-ion battery in the form of an ultra-long fibre that could be woven into fabrics. The battery could enable a wide variety of wearable electronic devices and be used to make 3D-printed batteries in virtually any shape.
The team has produced the world’s longest flexible fibre battery – 140 metres long – to demonstrate that the material can be manufactured to arbitrarily long lengths.
It was manufactured using novel battery gels and a standard fibre-drawing system that starts with a larger cylinder containing all the components and then heats it to just below its melting point. The material is drawn through a narrow opening to compress all the parts to a fraction of their original diameter, while maintaining all the original arrangement of parts.
Members of the team have previously demonstrated fibres that contain a wide variety of electronic components, including light emitting diodes (LEDs), photosensors, communications and digital systems. Many of these can be woven and are also washable, making them practical for use in wearable products, but all have so far relied on an external power source. The new fibre battery, which can also be woven and washed, could enable such devices to be completely self-contained.
Embedded
“While others have attempted to make batteries in fibre form, they were structured with key materials on the outside of the fibre, whereas this system embeds the lithium and other materials inside the fibre, with a protective outside coating making it stable and waterproof,” said MIT postdoc Tural Khudiyev, now an assistant professor at National University of Singapore. “This is the first demonstration of a sub-kilometre long fibre battery which is both sufficiently long and highly durable enough to have practical applications.”
A demonstration device using the new fibre battery incorporated a “Li-Fi” communications system – one in which pulses of light are used to transmit data – and included a microphone, pre-amp, transistor, and diodes to establish an optical data link between two woven fabric devices.
“When we embed the active materials inside the fibre, the sensitive battery components already have a good sealing and all the active materials are very well-integrated, so they don’t change their position during the drawing process,” Khudiyev said “ In addition, the fibre battery is much thinner and more flexible yielding an aspect ratio – the length-to-width fraction – of up to a million, which is far beyond other designs and makes it practical to use standard weaving equipment to create fabrics that incorporate the batteries as well as electronic systems.”
The 140-metre fibre has an energy storage capacity of 123 milliamp-hours, which can charge smartwatches or phones, and is only a few hundred microns in thickness.
Multiple devices
“The beauty of our approach is that we can embed multiple devices in an individual fibre, unlike other approaches which need integration of multiple fibre devices,” said MIT postdoc Jung Tae Lee, now a professor at Kyung Hee University. “When we integrate these fibres containing multi-devices, the aggregate will advance the realization of a compact fabric computer.”
In addition to individual one-dimensional fibres, which can be woven into fabrics, the material can also be used in 3D printing or custom-shape systems to create solid objects, such as casings that could provide both the structure of a device and its power source. To demonstrate this capability, a drone submarine was wrapped with the battery fibre to provide it with power. Incorporating the power source into the structure of such devices could lower the overall weight and improve the efficiency and range they can achieve.
The team has already applied for a patent on the process and continues to develop further improvements in power capacity and variations on the materials used to improve efficiency.
The development was reported in Materials Today and also involved MIT professors Yoel Fink, Ju Li, and John Joannopoulos, and seven others at MIT and elsewhere.
Business intelligence for the fibre, textiles and apparel industries: technologies, innovations, markets, investments, trade policy, sourcing, strategy...
Find out more