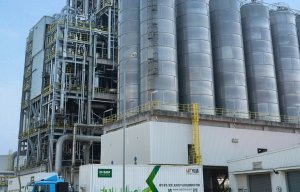
Loopamid now commercially available
Scaling up and pricing is very much dependent on the availability of PA6 waste feedstock.
10th April 2024
Innovation in Textiles
|
Munich, Germany
BASF wants your nylon fabric waste.
Speaking at the recent Performance Days Munich exhibition, Frank Reil, the company’s head of marketing, new business and sustainability for polyamides, outlined the work behind the development of its loopamid polyamide 6 (PA6 – commonly known as nylon 6), which is regenerated from 100% textile waste.
In January, Zara launched a jacket with all of its components – including fabrics, buttons, filling, hook and loop and zipper – made 100% from the new polymer.
At present, however, the feedstock for loopamid is mill waste.
“We would have loved it to have been based on recycled post-consumer waste because our recycling system is quite robust enough to handle it, but the reality is, such waste is simply not available,” Reil said. “Nobody can recycle it and the sorters can’t sell it, so they don’t look for it. To date we have been using off-cuts from production, which in many cases are already contaminated with dyes and finishes and often contain spandex.”
Sensor
Even the collection of PA6 mill waste was not initially without its problems, he explained.
The company specified 80% PA6 content but the first consignment received from its partner ModaRe, a take-back programme operated by the charity organisation Caritas in Spain, turned out to contain just 30%, since the sorting facility was unable to distinguish between PA6 and PA6.6.
This problem has now been resolved by the provision of an NIR (near infrared) sensor developed by BASF company trinamiX, which is able to effectively distinguish between the two polyamides, as well as identifying wool, cotton and polyester content.
Process
In the loopamid process, the 80% PA6-content waste is initially shredded prior to depolymerisation back to the raw material caprolactam. At this stage it is a brownish viscous liquid that is 20% non-caprolactam.
“There then follow a lot of purification steps to get it to the original caprolactam specification that is suitable for the production of new materials,” Reil said. “This means it is not a cheap process.”
Nevertheless, PA6 is made from just caprolactam, and not combinations of monomers like polyester, and it also has a much higher market value. The fibres and materials made with it can theoretically be recycled multiple times, with results identical to those of conventional virgin PA6.
In the creation of the Zara jacket, Inditex partnered with other leading groups in the clothing manufacturing industry to seamlessly integrate loopamid into various garment components, including fabrics, zippers, buttons, fillings, hook and loop fasteners and sewing threads. ModaRe classified, sorted and provided the mill waste and Italy’s RadiciGroup has been working to transform loopamid polymer into various types of yarn with different characteristics.
YKK and Velcro have also played crucial roles in utilising loopamid polymer to create plastic components for zippers, snap buttons and hook and loop fasteners. Uniter from Spain, Tessitura Vignetta from Italy and Freudenberg and Gütermann from Germany also participated in the project to develop other loopamid garment components such as inner labels, filling materials and sewing threads.
Reil said that commercial volumes of loopamid would be available by the end of 2024, but the scaling up from batch production to a continuous plant was very much dependent on the availability of PA6 waste feedstock.
“As sophisticated sorting and recycling grows in the EU, we expect this feedstock to become more widely identified and readily available, because right now the collection of the mill waste is super expensive,” he said. “This is preventing us from accurately forecasting a realistic market price for loopamid in commercial production.”
Business intelligence for the fibre, textiles and apparel industries: technologies, innovations, markets, investments, trade policy, sourcing, strategy...
Find out more