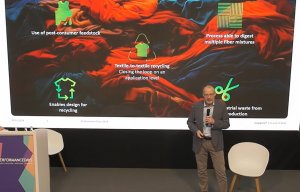
Chicken and egg situation for BASF’s new loopamid
First plant for GRS certified recycled polyamide 6.
11th April 2025
Innovation in Textiles
|
Shanghai, China
BASF has announced the start-up of the world’s first commercial loopamid plant with an annual capacity of 500 tons at its Caojing site in Shanghai, China.
Loopamid is a recycled polyamide 6 that is entirely based on textile waste. Currently, the feedstock is industrial waste from textile manufacturing collected and provided to BASF by customers and partners but the plan is to gradually increase the share of post-consumer waste.
End-of-life garments made from polyamide 6 and other textile products are challenging to recycle because they typically consist of a mixture of different fibres and materials as well as dyes and additives. Additionally, for post-consumer waste recycling, buttons, zippers and accessories must be removed in advance.
BASF is working closely with partners and customers to accelerate the development of collection and sorting systems.
“Loopamid transforms textile waste into a valuable resource, helps save raw materials and closes the textile loop,” said Stephan Kothrade, BASF CTO. “The new production facility supports the growing demand for sustainable polyamide 6 fibres in the textile industry.”
Global Recycled Standard (GRS) guarantees the content and the first yarn manufacturers are now successfully spinning the new fibre.
Business intelligence for the fibre, textiles and apparel industries: technologies, innovations, markets, investments, trade policy, sourcing, strategy...
Find out more