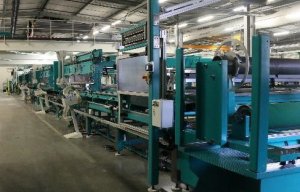
Chomarat invests in carbon multiaxial technology
Karl Mayer Malimo says its new generation Malitronic Multiaxial warp knitting machine is up to 25% more productive than its predecessor as the first machine goes on trial at a leading multi-axial fabrics manufacturer. According to Karl Mayer, multiaxial textiles made from high-performance yarns are on the rise, not only in terms of the volume produced, but also with regard to their range of end-uses. Multiaxial reinforcing textiles can be used as prepregs i
19th October 2009
Innovation in Textiles
|
Chemnitz
Karl Mayer Malimo says its new generation Malitronic Multiaxial warp knitting machine is up to 25% more productive than its predecessor as the first machine goes on trial at a leading multi-axial fabrics manufacturer.
According to Karl Mayer, multiaxial textiles made from high-performance yarns are on the rise, not only in terms of the volume produced, but also with regard to their range of end-uses. Multiaxial reinforcing textiles can be used as prepregs in wind turbines, aircraft and boats, and for repairing buildings, and Karl Mayer says they are revolutionising construction techniques.
Multiaxial fabrics are versatile textiles which can be tailored to suit the end product, and can also be given additional functions, enabling them to be used in a wide range of applications where a high load-bearing capacity is required. Karl Mayer says that the road from the initial idea to the end product leads via machine technology that offers the very best in terms of its economic aspects, flexibility and productivity, and Karl Mayer Malimo has taken these specific requirements into account fully in the development of the Malitronic Multiaxial.
According to Karl Mayer, as well as increasing the speed parameters, this new generation of machines also offers improved performance and consequently a higher level of efficiency. The productivity of this technically sophisticated machine has been increased by 20-25% compared to its predecessor and Karl Mayer says that on the other hand, the modular design concept of the Malitronic Multiaxial makes it extremely flexible.
“The Kamcos computer-based control system also ensures that all the process-relevant production parameters are optimally managed and transferred, and helps clients worldwide to guarantee the quality of their textiles on the basis of networked production technology”, the company adds.
The entire machine concept of the new Malitronic Multiaxial is a logical consequence of the demand for a modular design. Both the mechanical and electronic features of the individual components can be combined. Karl Mayer says that every individual module of the new multiaxial machine represents years of experience and know-how, is innovative right down to the last detail, and guarantees the quality of the Karl Mayer brand. The individual modules are built on a modern production line in the Chemnitz factory, are tested in accordance with strict specifications, and are assembled in the client’s factory once they have been certified.
As standard, the Malitronic Multiaxial is equipped with a continuous conveyor belt, which guarantees optimum delivery of the yarns for processing. As a replacement for the old type of belt arrangement, this full-width solution feeds the chopped glass mats uniformly and in specified manner, and also assists with feeding-in the weft layers that have been optimally pre-tensioned.
The distance between the conveyor belt and the bonding elements can be increased for easy access to the bonding point, without moving the yarn layers or the chopped glass mats. The extra space is created by moving the entire frame of the transport sheet backwards, without moving the conveyor belt in relation to the weft yarn sheet and without relaxing the tension of the conveyor belt. The conveyor belt can also be lowered or raised over its entire length. Adjusting the height of the transport surface prevents the thick, chopped glass mats from being distorted or squashed by the laying device of the weft laying system, or by the yarn bands that have to be inserted. Optimising the entire transport system thus ensures that the textile has an attractive appearance and makes the machine more user-friendly.
The wide cutting unit is an optional feature for producing the chopped glass mats. A roller having blades arranged horizontally on its surface, with a distance between them that corresponds to the length of the fibres that has to be produced, is used for chopping the glass rovings that are delivered. The cutting point is supplied downwards via an optimised system consisting of a pressure roller and a rubber-coated seal to produce a counter pressure. The cut fibre pieces trickle downwards and pass over a rotating distributor roller to distribute them more evenly to form a homogeneous mat, either directly onto the conveyor belt if the production of a chopped fibre mat is the first stage in the production process, or onto the unbonded layers of reinforcing yarns, close to the location of the cutting unit just in front of the stitch-bonding point. The customer can decide what sort of wide cutting system they require, depending on whether the glass mat is incorporated on the top or bottom of the textile.
The compensating yarn tensioner equalises any differences in yarn consumption whilst the reinforcing yarns are being laid. At the reversal points, at which the weft laying system is braked, the component having two yarn guide systems that can move relative to each other, takes up the yarn material and this gives rise to two advantages: constant take-off of the yarn from the package, and the release of yarn material on the basis of the yarn consumption at the laying device to avoid differences in tension. This ensures that the tension in all the yarns is uniform during the entire weft insertion. As part of the work on optimising the machine, the compensating yarn tensioner was fitted with an ionisation rod to increase the process reliability.
The weft laying system is responsible for the sheet-wise positioning of the reinforcing yarns in accordance with the angles that have been set for the weft laying device. The weft laying devices can be adjusted step-wise in increments of 1° between -45° and +45°. The Malitronic Multiaxial is normally equipped with three weft laying systems, but may be equipped with a maximum of five. Every one of the components used in yarn laying has been designed as separate units, so that they can be removed or integrated as required, and they also have their own control unit. In line with this modular design, the weft insertion frame is also made up of segments.
The weft laying system has been stabilised to reduce wear and tear on the construction, which is subject to high levels of stress, and to make weft insertion even more precise. An optimised drive system also helps to improve the laying quality and also makes the system more efficient. A characteristic feature of this system is the positioning of the motors on the laying device, i.e. the individual motors are located close to the point of operation. This new solution, which has fewer mechanical elements, improves positioning and this increases the weft laying frequencies, the shog width and reduces waste.
The transport chains on the longitudinal sides of the weft insertion frame receive the reinforcing yarns at the reversal points from the weft laying devices and transport the yarn layers to the bonding point. Horizontally and vertically arranged needled pins are used to fix the weft yarns in place. The needled segments reliably absorb the tensile forces resulting from the optimum yarn tension levels. For this purpose, the entire chain with its superstructures has been stabilised. The drive has also been optimised. The transport chains used to be moved by a motor, in which case the tension was distributed by a complicated, coordinated mechanical system. Two electric motors, which are electronically synchronised, are now responsible for the drive and tension distribution. The advantages of separating these two systems include simpler handling, the production of a high quality textile, and exact reproducibility of all the main settings.
The delivered reinforcing material is bonded at the bonding point by the formation of stitches. The gauge is designated by the letter E rather than F, and relates to the number of needles per 25.4 mm, as is normal in warp knitting.
The design of the elements for delivering the filler thread to the bonding point has been simplified and optimised, and it now guarantees accurate material feed at a constant tension.
A new roller covering enables a yarn sheet to be fed over each of the four delivery rollers. Looping over two rollers is no longer needed. The extra space that this frees up enables the yarn sheets to be delivered separately and accurately and they do not impede each other in any way. Four electric motors, one for each delivery roller, are responsible for 100%-accurate regulation of the tension, and these can be controlled exactly.
After leaving the bonding point, the unbonded selvedges are cut off, sucked away and collected. On the predecessor to the Malitronic Multiaxial, the edges that had been removed were collected in waste bins at both sides of the conveyor belt for intermediate storage, a labour-intensive process. The process has now been simplified by using a central waste bin, which is filled with the selvedge waste from both sides of the textile via a tubing system. Once the waste in the container has reached a specific level, the waste automatically falls into a trolley for easy removal. The number and position of the knife discs for cutting the edges, together with additional rotating cutting tools, can be adjusted as required along the working width to cut the textile into strips to suit the end-use.
Fabric take-down is carried out as standard with 2 and 3 roller take-down units. Depending on the type of article being produced, the user can use the appropriate take-down system without having to go to the time and trouble of changing over the entire system. The fabric take-down system, just like the fabric batching system, is designed as a separate module.
For the time being, fabric batching is the final stage of the production process carried out by the new Malitronic generation of machines and the Multiaxial type. The standard component for surface winding for taking up the final textile operates semi-automatically, and thus helps to save time when removing the textile roll. The starting point for making this system more efficient was the process involved in raising the pressure roller. This relatively time-consuming process has to be carried out in order to change the roll. It used to begin once the specified running length had been reached, but now begins at a point in time that can be specified by the operator in advance. Once the roll is full, the pressure roller has already reached its upper position and the roll is automatically ejected. This saves time and frees up the operator to do other things. A further reduction in the stoppage time associated with roll changing can be achieved by installing a textile storage device.
A combined surface and central winder having extended functions is available for carrying out the winding process when the quality of winding must meet stringent specifications, for winding sensitive materials, or for winding long lengths.
With the new Malitronic generation of machines, Karl Mayer says it can thus supply just the right components for the entire production process, from the package to the final roll, and this will help the company’s customers as they face the future. The innovative solutions guarantee that high-quality textiles are produced and that every available resource is used economically, the company says.
The wide range of different, high-quality multiaxial textiles that can be produced on the Malitronic Multiaxial is setting the trend on the market and opening up new applications. One of these innovative machines is available in Karl Mayer’s technical centre for developing new products in conjunction with clients, as well as for training purposes. Another machine is currently demonstrating all its capabilities as it undergoes industrial trials in the plant of a multiaxial textile producer.
Business intelligence for the fibre, textiles and apparel industries: technologies, innovations, markets, investments, trade policy, sourcing, strategy...
Find out more