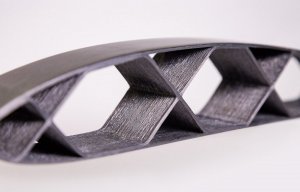
Continuous Composites recognised by Sikorsky
Overcoming the challenges of winding large components in high volumes.
5th April 2022
Innovation in Textiles
|
Northwich, United Kingdom
Fibre handling and converting technology specialist Cygnet Texkimp, based in Northwich, UK, will showcase its high-speed multi-axis winder (MAW) at JEC World, taking place in Paris from May 3-5 2022.
With both live demonstrations and a conference talk, the company will explain how its MAW can change the way continuous parts can be manufactured at speed, overcoming the challenges of winding large components in high volumes.
Technical manager Andy Whitham will discuss the application of component winding technologies for multi-purpose industry solutions at 9.30am on Thursday May 5th in the Composites Exchange forum.
“JEC provides a unique platform to showcase this technology that allows for a high volume of material to be put down at speed,” he says. “My talk will be a deep dive into the techniques being developed by Cygnet Texkimp to facilitate high speed filament winding and will give an opportunity for attendees to ask any questions.”
The multi-axis winder (MAW), developed in conjunction with the University of Manchester, will be showcased to attendees on its merits for enhanced capability in winding tow-pregs, thermoplastic tapes and dry fibres such as carbon, aramid and glass.
The MAW focuses on the production benefits associated with the technology and complements the company’s 3D Winder, used for complex, curved composite parts.
The static mandrel of the MAW is designed to be integrated into an automated manufacturing system able to efficiently wind linear structures such as tubes and profiles of varying sizes. Thanks to balanced fibre tensions around each part, the static mandrel (or former) needs little strength and can therefore prove inexpensive. Its implementation with robotic loading and unloading technology allows parts to be continuously manufactured, wound and stored to provide a turnkey manufacturing cell. This process is capable of a faster and more accurate alternative to conventional braiding and filament winding.
In addition, Cygnet Texkimp will exhibit its Deecom waste recycling solutions technology using superheated steam to remove polymers from composite fibres and allowing for raw materials to be reused in the manufacturing process. The steam is cycled through a pressure vessel to gently remove resin matrices from fibres in a controlled environment. The expelling of clean H2O reduces the carbon footprint and acts as an alternative to pyrolysis incineration, while the re-use of high-performance, pristine clean fibres puts an end to excessive material wastage like prepreg offcuts and the process and transportation for landfill.
The technology will benefit machines such as the MAW to streamline waste disposal and improve the environmental impact of the automated production cell.
“We are excited to be reuniting with the industry and exhibiting our latest solutions for composites manufacturing,” said Luke Vardy, Cygnet Texkimp CEO. “On behalf of the team I welcome all to join us at our stand M72 in Hall 5.”
Business intelligence for the fibre, textiles and apparel industries: technologies, innovations, markets, investments, trade policy, sourcing, strategy...
Find out more