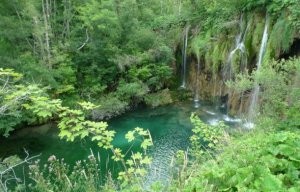
Freudenberg introduces Eco-Check product label
Opinion
Future Fabrics Expo showcased next gen materials and alternative dyeing methods, while providing a platform to discuss the path to circularity.
4th July 2024
Anne Prahl
|
London
Future Fabrics Expo 2024, held from 25th-26th June in London, featured an extensive selection of commercially available lower impact materials for fashion, footwear and home products, while continuing to showcase emerging and future material and process innovations.
Next Gen material innovation
The buzz around ‘Next Gen Materials’ continues, as an ever-growing number of innovators present recycled, renewable and lower impact material alternatives to the fashion industry’s most ubiquitous materials including virgin polyester, cotton and leather. However, we have now reached a stage where questions about scale-ability and commercial adoption, as well as the role of next gen materials in achieving circularity are discussed more frequently.
Polyester textiles made from recycled single-use plastic bottles were seen as a ground-breaking solution when they first emerged in the early 1990’s, and many sportswear and fashion brands have adopted recycled polyester over the last decade. Due to a growing number of environmental and health concerns, this bubble has now burst and calls to move away from single-use plastic waste towards textile-to-textile recycled feedstock are getting louder.
As more mechanical and chemical textile-to-textile recycling technologies are being developed and scaled-up, the expo also highlighted that textile and garment manufacturers are beginning to set up in-house hubs to recycle their own textile waste and utilise textile waste as a feedstock in their products.
Spanish textile company Torné Grup reuses cotton waste generated during their textile production process to spin recycled yarns for new woven interlinings, while Swiss company Säntis Textiles collects fabric cuttings and yarn waste to create virgin-like mechanically recycled cotton bales, which are spun into cotton yarns. The company are also making their patented recycling machines available to other manufacturers to enable in-house textile waste recycling.
Recyc Leather presented their new material PELINOVA, which combines post-industrial leather waste fibres and TENCEL™ Lyocell fibres into a flexible and durable leather alternative by utilising a mechanical punching process. This process uses 70% less water and reduces CO2 emissions by at least 18 times, compared to conventional leather production.
Driven by the move away from plastic, innovation around biobased raw materials is unstoppable and there is a constant stream of new fibre and fabric developments derived from plant-based materials and agricultural waste feedstocks, as well as regenerated cellulosic.
Although environmental organisation Parley for the Oceans was a strong force behind ocean plastic recycling through their partnership with adidas, the company does not consider plastics recycling as the ultimate solution. Parley is now on a mission to support the scale-up of natural and bio-fabricated materials as an alternative to fossil-fuel derived textiles and showcased a clothing collection made with biomaterials from innovators including Bananatex, TômTex, Ponda and Nature Coatings.
Textile innovation start-up Fiiba is developing cotton and viscose replacements made from up to 100% agricultural banana waste, a food industry by-product. The manufacturing process reduces greenhouse gas emissions by 90% compared to organic cotton and viscose, while production by-products including pulp and organic fertiliser go to paper-making partners and farmers.
Material innovator HeiQ has been exploring a wide range of feedstocks, including pre- and post-consumer textile waste, bacterial cellulose, and cellulosic agricultural waste, such as orange peels, coffee grounds and pineapple leaves to develop their HeiQ AeoniQ cellulosic filament yarn. This yarn, which will be ready for commercial use by 2028, is designed as an alternative to cotton and polyester and is eternally recyclable, as well as biodegradable within 12 weeks at the end of its lifecycle.
Biomaterials company Ponda’s BioPuff insulation is made by transforming seed heads from the Typha Latitolia, a native, shallow-water plant, which thrives in freshwater and marshes, and is an ideal low-maintenance crop for wetland restoration. Qualities presented at the expo ranged from 40-80% Typha fibre combined with 60-20% recycled polyester and the material is equipped with enhanced biodegradability.
Innovators are also investigating how to combine material production with product manufacture, as this can result in significant energy and waste reduction. US based material innovator Simplifyber has developed a manufacturing process where plant-based or recycled textile fibres are poured as a liquid slurry of fibres and water into a system of moulds to produce 3D-shaped products. At end of life these products can be recycled into paper or card and are also biodegradable.
London based start-up Weffan’s 3D woven garment production system merges the weaving of the fabric with the creation of the product to reduce production waste. In addition, this technology can be used to enable recycling at end-of-life, as specific parts, such as shirt collars and cuffs, can be constructed as one mono-material piece, therefore eliminating the need for fused interlining.
Re-thinking dyeing methods
While raw materials are key enablers of product circularity, innovators are also working on cleaning up the traditional dyeing process to reduce environmental impact and improve resource efficiency, as well as eliminating potential inhibitors to recycling.
DyeRecycle Synthetics is a circular solution for recovery and recycling of dyes from synthetic textile waste and allows dyes to be reused for colouration, while providing decoloured and clean textile waste fibres, ready to be mechanically or chemically recycled. The company also offers DyeRecycle Cellulosics, a process which disintegrates cotton into a cellulosic powder, which can be used as a pigment for new fabrics.
With the aim to support the wool industry’s transition to a circular system, researchers at De Montfort University and Loughborough University are currently developing enzyme-based biotechnologies to separate and extract dyes from waste wool textiles. The dyes are recovered in powder form and can be reused to dye new textiles.
Biotech start-up Werewool are driven by the aim to eliminate plastics and pollution from the dyeing process and look to nature for inspiration. The company’s process involves the engineering of proteins at DNA level to create fibres with inherent bright colours and functional properties, including elasticity and moisture management.
Biotech company Post Carbon Lab specialise in leveraging photosynthetic microorganisms, such as cyanobacteria and algae, to create high performance microbial colours for a wide range of textiles. The company has now collaborated with natural dyehouse True Tone Ink to develop and launch a collection of climate positive microbial-herbal shades for commercial use.
The path to circularity in fashion
While the amount of alternative material innovation is inspiring, the expo raised important questions whether and how some of these solutions can sit within a truly circular fashion system.
There are growing calls for brands to invest in next gen textiles early and widely to successfully scale and commercialise them. However, many of these innovations are not recyclable, as they are made from diverse and unsupported feedstocks, for which recycling technologies do not exist. This may create difficulties for companies needing to adhere to eco-design requirements, such as incorporating product recyclability to comply with upcoming EU textile regulations, and the concern is whether the demand for cotton and polyester textiles will further increase as a result, as these will be supported by existing and emerging recycling technologies.
Panellists further highlighted the need for collaboration between what may be seen as competing technologies or companies to build platforms for positive change. Textile-to-textile recycler Circ recently launched Circ-Ready, a community of global supply chain partners, who are given the opportunity to replace virgin inputs with Circ’s pilot-stage products. Examples of this collaboration include Spanish R & D company Pyratex’ Circ lyocell fabric and garments created by Pakistan’s largest denim maker and exporter Soorty.
To drive circularity in fashion, it is essential to support textile-to textile recycling innovators and seminar panellists sent a clear message that while investment and feedstock are the smaller challenges, what is still lacking is the demand and commitment from brands. This point is illustrated by the recent obstacles textile-to-textile recycling company Renewcell had to overcome, resulting in having to rebrand as Circulose under new owners.
A final thought-provoking point was raised during one of the panels, when author and director of clothing brand Community Clothing Patrick Grant stated that material innovators are facilitators of the high level of clothing output, at a time when the industry needs to address overconsumption and explore approaches that reduce the production and consumption of clothes.
Business intelligence for the fibre, textiles and apparel industries: technologies, innovations, markets, investments, trade policy, sourcing, strategy...
Find out more