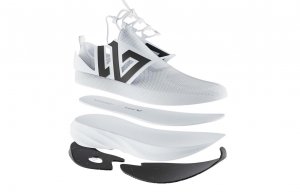
Sustainable focus for ISPO sports winners
Opinion
ISPO 2022 showcases a wide range of recycled and bio-based materials, and solutions to accelerate the transformation to a circular sports and outdoor industry.
6th December 2022
Anne Prahl
|
Munich, Germany
After an enforced three-year absence, sports trade fair ISPO Munich returned under the motto ‘New perspectives on sports’, which aimed to examine topics including technology, sustainability, diversity and retail. From a material and product perspective, the focus on sustainability continued to grow in importance, as fabric suppliers and brands showcased a wide range of recycled and bio-based materials, as well as presenting solutions to accelerate the transformation towards a circular sports and outdoor industry.
Recycled textiles trend continues
Following industry-wide commitment to reduce the reliance on virgin fossil fuel based raw materials, sports and outdoor brands have rapidly increased the use of recycled synthetics. As recycled polyester and polyamide performance fabrics made from single-use plastic waste are becoming mainstream, rather than being considered an exceptional sustainability feature, brands are looking to explore additional innovative feedstocks and sustainability features.
Spanish outdoor brand Ternua’s ISPO Award winning baselayer SEAL L/S t-shirt is made from recycled nylon manufactured out of discarded, locally collected fishing nets, and produced in the brand’s own factory in the Pyrenees. The t-shirt has been equipped with odour-inhibiting HeiQ Fresh MNT finish, which, as it is based on mint oil, is a welcome alternative to metal-based antibacterial treatments.
Another ISPO Award winner in the baselayer category is Austrian knitwear specialist Löffler’s transtex underwear. The collection is produced with recycled polypropylene made from leftover textile cuttings, and unbleached and undyed recot2 cotton made with 25 percent recycled cotton and 75 percent GOTS-certified organic cotton. The material benefits from a two-layer knit construction, which enables the polypropylene on the inside to transport moisture away from the skin, while the second layer stores and releases it to the outside, allowing for natural body temperature regulation.
Outdoor brand Vaude have collaborated with chemical company BASF to develop a chemical process, which can produce polyamide fabric from discarded car tyres. The recycled fabric is as durable, fast-drying and high-performance as conventional polyamide and saves 60 percent of CO2 emissions during production, compared to materials relying on the extraction from fossil fuel.
Norwegian wool specialist Aclima’s collection ReBorn is made from a fabric blend of 70 percent recycled wool manufactured with the company’s own production off-cuts, and 30 percent recycled polyamide. Original developments aimed for 100 percent wool, but the addition of recycled polyamide allows for better garment durability, while providing an appealing melange effect, which eliminates the need to redye the wool.
Recycled insulation options are also on the increase and examples showcased at ISPO included recycled down, cashmere, wool, and textile waste. Allied Feather + Down introduced their new Renu:Trace recycled and traceable down insulation program, which complies with Responsible Down Standard protocol to guarantee ethical production and animal welfare.
Re:Down source most of their down and feathers from textile waste collectors, before they are regenerated into insulation for new products, such as padded jackets, sleeping bags or bedding. In line with the company’s Zero Waste policy, they are working with French start-up Iteratif to enable full circular solutions for down jackets. This includes the removal of fabrics, zips and buttons, so that all components can be recycled. In addition, Iteratif’s software system provides full traceability for each material and can therefore help brands to improve the recyclability of their products.
Steps towards Circularity
While the sports and outdoor industry has begun to embrace the concept of circularity, it is becoming painfully clear that the transition to a circular industry is a slow and challenging process, which relies on ongoing innovation and collaboration between various strategic partners.
Suisse brand Muntagnard’s collaboration with Innovation Unit resulted in the ISPO Award winning MIUtec Iso jacket, which, thanks to durable material and timeless styling, is designed to have a long life but is also recyclable and/ or biodegradable at end-of-life. Materials include enhanced biodegradable polyamide 6.6 for the shell, linings, pockets and trims, in combination with 100% lyocell insulation.
Other products designed with circularity in mind by following a mono-material strategy are Ternua’s 100 percent polyester based AGILE HYBRID JACKET and German outdoor brand Schöffel’s CIRC Pants LOOOP, which can be recycled through the patented RevolTEX process at end-of life.
While strategic material choice can enable recycling or composting at end-of-life, the first rule of circularity should be to design products for multiple and extended product lives. This can be achieved through durable material use and classic design but also needs to be supported through rental, repair or reconditioning services. Many outdoor brands are offering such services and French snowsports brand Picture are no exception. The brand launched their rental program in 2021 and from S/S 23, they will offer a lifetime repair warranty on all technical pieces as part of their Circular program.
Two Japanese companies showcased their chemical polyester textile-to-textile recycling technologies. Jeplan’s ‘Clothes to clothes’ BRING Technology, which is described as infinitely recyclable, and Toyota Tsusho Corporation’s textile-to-textile technology rely on a process of decolourisation, depolymerisation, repolymerisation into pellet chips and spinning into new polyester yarn. Toyota Tsusho also recently announced their support of Patagonia’s Tee-Cycle circular service and the company have begun to work on separating and classifying collected cotton products in preparation for recycling them into new products.
To achieve the ultimate goal of fibre-to-fibre recycling there are still various challenges to overcome. Progress is obstructed by the use of complex material blends, certain chemicals in dyes, prints and performance finishes and high contents of elastane. A growing number of innovators and fabric mills are developing alternative solutions, which can eliminate some of these obstacles to enable efficient recycling at end of product life.
UK start-up Amphico demonstrated Amphitex, the first 100% recyclable and chemical-free alternative to traditional waterproof, breathable outdoor performance textiles. The company’s Amphidry yarn on the face of the fabric is inherently hydrophobic and requires no water repellent coating. The material can be made into a highly waterproof and breathable membrane, and as all layers within Amphitex are made from the same polymer, the textile can be recycled.
A growing number of fabric mills can now engineer stretch and recovery through construction, so they are more easily recyclable at end-of-life. Great examples of this approach are fibre manufacturer Hyosung’s regen xanadu fabric, which is made with a blend of recycled post-consumer PET and corn-based materials, and yarn producer Nylstar’s and circular knitting machinery manufacturer Santoni’s collaborative concept garment. The garment marries Nylstar’s natural elasticity yarn, which does not require elastomers to provide stretch, with Santoni’s seamless knitting technology.
Increased innovation in bio-based materials
Bio-based textiles are rapidly growing in popularity, as designers and developers are searching for alternatives to fossil-fuel based performance textiles. Italian brand UYN attracted much attention with their Bio Lab display, which featured an impressive vision of what nature empowered performance sportswear can look like.
The brand’s new EVOLUTYON BIOTECH technical baselayer set won the ISPO Award for its use of 100 percent bio-based materials, which combine Kapok, Biolight yarn derived from the cellulose of beechwood trees, Flexicorn yarn made from corn seeds, and Natex yarn, produced from castor oil seeds.
As the first company to commercialise bio-based elastane, Hyosung presented a range of textiles and garments made with creora bio-based elastane, which replaces 30 percent of petroleum-based resources with bio-based materials derived from industrial field corn. Hyosung are planning to introduce a 70 percent bio-derived version next year, aiming for a full 100 percent, without stretch or recovery loss, in the future.
To produce the required raw materials, Hyosung has partnered with US based CovationBio, who make partially plant-based polymer Sorona and Susterra, the 100 percent plant-based PU ingredient. The company produce their annually renewable industrial corn in the United States, where farmers use regenerative agriculture to restore terrestrial ecosystems.
Another notable move towards petroleum-free performance materials is Polartec’s new bio-based version of its breathable and waterproof Power Shield fabric technology. The technical membrane is 48 percent bio-based and outperforms any breathable and waterproof technologies the company have previously created. In addition, the product is more durable and therefore enables consumers to keep their performance garments in use for longer.
Business intelligence for the fibre, textiles and apparel industries: technologies, innovations, markets, investments, trade policy, sourcing, strategy...
Find out more