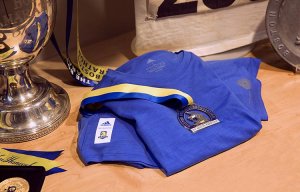
adidas and Woolmark explore new product applications
Direct-to-textile 3D printing was first demonstrated by designers at New York Fashion Week in 2019, with the latest achievement of printing directly onto wool an industry first.
2nd September 2021
Innovation in Textiles
|
Milan
Ahead of next week’s Milan Design Week, D-house, an urban laboratory where pioneering research and development is carried out using cutting-edge technology to inspire and guide designers in the discovery of new fashion applications, has been exploiting the latest Stratasys direct-to-textile 3D printing technology.
The resulting collection, Knitting the Future. 3D Printing meets Merino Wool, was developed with The Woolmark Company, a non-profit authority on Australian wool, and Stratasys, a global leader in 3D printing.
D-house was created by Dyloan, a leading Italian manufacturer serving the high-end fashion sector since 1987, known for adopting new technologies for design applications with fashion brands.
Unique patterns
For this latest collection, three international designers and four students from the Royal College of Art in London, supported by several Italian knitters and spinning mills, successfully 3D printed unique patterns directly onto Merino wool knitwear using PolyJet J850 3DFashion technology.
On the materials side, I believe that over the coming years we will not necessarily have to use fabrics. New materials will emerge, and with direct-to-textile 3D printing we will be able to use them to produce a new category of garment
Stratasys direct-to-textile 3D printing was first demonstrated by designers at New York Fashion Week in 2019, with the latest achievement of printing directly onto wool an industry first.
Among the most inspiring outfits in the collection is Illusion, a stylish jacquard coat with a four-color 3D effect created by designers Vittorio Branchizio and Uroš Mihić in collaboration with Maglificio MAS. The texture of the 3D print, echoing dice, creates the illusion of iridescent shades of color, in an optical game that changes according to the perspective observed. To achieve the eye-catching chromatic effect, the designers 3D-printed an array of hollow cubes directly onto the back of the jersey knit coat. They were then arranged in a precise configuration to enable the surfaces to filter color, creating a change in tones and shades. The designers added a thermosetting thread to the 100% Merino wool fabric to provide additional structure to the garment.
Another equally elegant creation is //WOOOL//, by designer Matteo Cibic in collaboration with Maglificio Miles, which comprises both male and female outfits in his elegant and creative design style. Both pieces are made from pure Merino wool yarns and feature a series of 3D effects directly printed onto the fabric. Key to the concept, was the use of 3D printing to produce transparent volumes, housing internal shapes to create a holographic effect. Using PolyJet J850 3DFashion direct-to-textile 3D printing technology, Cibic was able to create a series of ultra-clear 3D structures. These feature thin internal strips of contrasting patterns and colors, applied directly to the Merino wool. The result achieved by the transparent lens-like structure offers different perspectives of the images.
Colour accuracy
“What immediately surprised me about this 3D printing technology is the Pantone color accuracy,” explains D-house founder Loreto Di Rienzo, who runs the company with his sister Anna Maria of Dyloan. “We can create the required colour in extreme fidelity – a non-negotiable when working with fashion creatives,”
“In addition, the diverse material properties available allow us to take our freedom of design to the next level. Not only can we directly 3D print different textures and finishes onto the item, we can also include functional elements to the garment. Having these capabilities allows us to present customers with a range of outstanding aesthetics and highly creative alternatives.”
The strides made to date in unearthing new fashion design possibilities using PolyJet J850 3DFashion direct-to-textile 3D printing technology has not gone unnoticed, with Di Rienzo confirming discussions with several leading fashion brands on new upcoming projects.
The team at D-house is also exploring entirely new production methods for high fashion garments, bags and shoes, including the combination of direct-to-textile 3D printing with other processes such as thermoforming, as well as the use of the technology to repair vintage garments to further increase sustainability within the industry.
Complex geometries
“3D printing allows us to produce complex design geometries not possible any other way, and my dream is to create a finished garment made entirely with 3D printing,” says Di Rienzo. “The technology has decorative and functional properties that we are currently exploring, which I have no doubt will enable us to achieve new and unexpected applications. On the materials side, I believe that over the coming years we will not necessarily have to use fabrics. New materials will emerge, and with direct-to-textile 3D printing we will be able to use them to produce a new category of garment.
“Also, from a sustainability perspective – a key issue in the world of high-end fashion – 3D printing gives us the ability to customise and produce pieces in only the exact quantities needed. This is one of the reasons why we have a close partnership with Stratasys, which is crucial to our business moving forward.”
According to Naomi Kaempfer, creative director for art, design, and fashion at Stratasys, the company is focusing on producing 3D fashion garments that will be sold commercially in the luxury and haute couture market, and that comply with the high-performance standards of exclusive brands.
“Over the past five years, we’ve seen 3D printing make headlines with our fashion design collections,” she said. “Collaborating with high end fashion brands, we are focusing on demonstrating novel computed aesthetics which trigger optical illusions. This, together with highly intelligent 3D design software, is raising the bar with a new design language for the fashion market.”
Business intelligence for the fibre, textiles and apparel industries: technologies, innovations, markets, investments, trade policy, sourcing, strategy...
Find out more