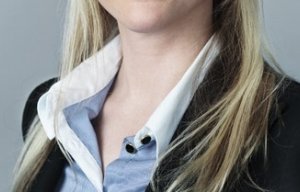
Spinnova appoints new Head of Communications
Spinnova fibre originated from work to emulate the production of spider silk and spin filaments from cellulose.
13th October 2021
Innovation in Textiles
|
Finland
Spinnova and VF brand Icebreaker are developing circular midlayer products with next-generation blends of merino wool and the highly sustainable Spinnova fibre that can be recycled again and again.
The blend Spinnova and Icebreaker are now piloting is sustainable and comfortable and also fully circular. After consumer use, the developed yarn is intended to be separated and reused, with the ambition of getting one step closer to circularity and lowering impact on the environment.
Icebreaker is an industry sustainability pioneer with ambitious sustainability goals, including abandoning the use of plastic fibres by 2023. Already in 2020, 91% of Icebreaker’s materials were merino or plant-based.
“The potential to recycle Spinnova into a new fibre again and again makes this disruptively circular,” said Alistair Smith, director of global product design at Icebreaker. “This partnership drives forward sustainable design.”
No dissolving chemistry
Speaking at the recent 60th Dornbirn Global Fiber Conference (Dornbirn-GFC) that took place from September 15-17, Spinnova’s CTO Juha Salmela explained how the Finnish company is taking a different approach to cellulosic fibres and stressed that its production involves no dissolving chemistry.
The development of Spinnova fibre originated from work to emulate the production of spider silk and spin filaments from cellulose.
The company was spun off from the VTT research centre and built its first pilot scale plant in 2019, becoming a public company listed on the Helsinki stock exchange last year.
Spinnova technology enables fibre production from wood but also from textile waste or agricultural wastes such as wheat straw.
The process is said to use no harmful chemicals and 99% less water than the cotton value chain. The fibre creates minimal CO2 emissions in production, is quickly biodegradable and contains no microplastics.
Fibres are based on wood, but also waste textiles and leather and the process involves pulping before mechanical grinding, with no dissolving pulp needed. Elementary fibrils are released in the process via patented spinning nozzles and the water is evaporated out. As such Spinnova technology is a dry spinning process with no washing cycles involved.
Spinnova has now partnered with Suzano, the world’s largest wood eucalyptus pulp producer to build Respin, a commercial scale fibre plant in Finland, with output to become available in 2022.
The Respin production with Suzano will be based on pulp but Spinnova is also developing a second technology platform with Helsinki-headquartered KT Trading, owner of the best-selling Ecco shoes brands, based on leather waste, called Woodspin. This production route could switch from leather waste to textile waste without having to be changed.
Business intelligence for the fibre, textiles and apparel industries: technologies, innovations, markets, investments, trade policy, sourcing, strategy...
Find out more