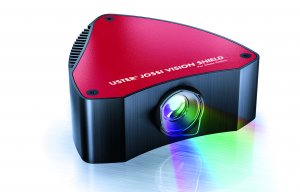
System gains from customer feedback
The Uster Jossi Metal Shield’s technical advantages could bring a cost reduction of more than US 7,000 per year, according to the manufacturer.
27th February 2015
Innovation in Textiles
|
Uster
Every spinning mill needs to invest to maintain its competitive edge. Keeping pace with latest technology is paramount – but too much emphasis on the actual production machines can also be risky, especially if the spinner fails to protect a new investment adequately, the company believes.
Expensive production machinery such as cards and spinning frames can easily be damaged, for example, by metal pieces caught up in the fibres. The resulting impact in terms of downtime and substandard yarn quality can be costly.
According to the manufacturer, one of the most often seen incidents in spinning mills involve a problem in the card that was caused by a metal piece being transported and forwarded with the cotton tufts.
These metal pieces that get into the mill could be screws, nuts, travellers, pieces of wire or metallic bale strapping that might find their way into the cotton in various manners. Anything carelessly dropped on the floor in these situations could be swept up and entangled with the cotton – even in the tidiest of mill environments.
The best protection method available to a mill, the company reports, is to install an instrument for metal detection and elimination shortly after the bale opener. A daily average of 10 to 20 metal pieces is taken out of the yarn production process in this way, but the figure can sometimes reach up to 50.
That means the instrument’s diverter mechanism opens as many as 50 times a day, each time sending the raw material stream containing the detected metal piece safely along a side channel for disposal.
For spinners this kind of procedure leads to wasted raw material, the company reports. With conventional instruments of this type, the diverter opens for three seconds at each detection – so a total of 90 seconds per day with 30 incidents. This produces 20 kg of wasted cotton, worth at least US 24 today.
The Uster Jossi Metal Shield, however, has a number of exclusive technical advantages which would, in the same example, result in only 2 kg of waste. A key feature is its use of inductive sensors, which not only detect the metal piece but, at the same time, measure its mass and speed.
Based on this, the opening time of the diverter is adapted, in a range from 0.2 to 3 seconds. Since only one in 30 metal pieces requires the diverter to open for the full 3 seconds, the shorter total opening time and the ensuing savings improve the mill’s profitability. Thanks to this feature, known as Speedsense, the Uster Jossi Metal Shield typically brings a cost reduction of more than US 7,000 per year, according to the manufacturer.
Business intelligence for the fibre, textiles and apparel industries: technologies, innovations, markets, investments, trade policy, sourcing, strategy...
Find out more