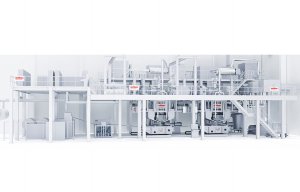
ecuTEC+ significantly improves filter performance
Highly-sophisticated nonwovens for filtration can be based on a wide range of polymers.
9th February 2022
Innovation in Textiles
|
Neumünster, Germany
Oerlikon Nonwoven, headquartered in Neumünster, Germany, will be making its debut at this year’s Filtech, the major trade fair for filter and filtration systems which takes place in Cologne, Germany, from March 8-10, 2022.
Unique and highly-sophisticated nonwovens for filtration can be simply and efficiently manufactured using the company’s meltblown technology based on a wide range of polymers, from classical polyolefins (PP, PE), PET, PLA, PBT and PA through to special plastics such as PPS and TPU.
Visitors to the company’s stand can also discover how filter media can be efficiently electrostatically charged with the ecuTEC+ electro-charging unit for increasing the filtration performance of meltblown media without reducing air permeability. This unit distinguishes itself from other concepts currently available on the market with its extreme flexibility, allowing users to set the optimum charge intensity for their specific filter applications.
“EcuTEC represents the beginning of an era of new charging and treatment systems available from Oerlikon Nonwoven for further increasing media filtration performance and product diversity,” said Dr Ingo Mählmann, head of sales at Oerlikon Nonwoven.
The company’s systems for industrial nonwovens are also capable of high production capacities and yields with simultaneously low energy consumption. In addition, spunbond products are also becoming increasingly important in filtration applications – both as backing materials for filter media and as the filter media itself. An engineered nonwoven structure permits the inclusion and/or combination of different customer-specific requirements for various functions into just one layer.
Oerlikon’s many years of bicomponent spinning experience enable the creation of completely new nonwoven structures and hence the incorporation of various functions in a single material. The bicomponent spinning process allows for the combination of various fibre cross-sections and the manufacture of different fibres from single or different polymers using only one system. The spectrum ranges from classical core-sheath and side-by-side bicomponent filaments and splittable fibres through to so-called mixed fibres.
Business intelligence for the fibre, textiles and apparel industries: technologies, innovations, markets, investments, trade policy, sourcing, strategy...
Find out more