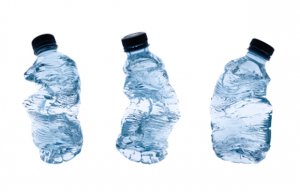
Unifi recycles 10 billionth bottle
More than half of the annual production of 45 million tons of PET used today is processed into manmade fibres.
10th November 2014
Innovation in Textiles
|
Remscheid
Today, over 200 billion bottles of water are drunk every year and bottles made of synthetic materials have virtually replaced glass as a packaging material for water and other drinks.
Bottles made of synthetic polyethylene terephthalate (PET) are not only practical and unbreakable but because of their low weight, transporting them also consumes less energy. A further advantage is that the material can be easily recycled.
More than half of the annual production of 45 million tons of PET used today is processed into manmade fibres. These make wrinkle-free and tear-resistant textiles, which absorb very little water. They are, therefore, ideal for clothing that needs to dry quickly and such fibres are also used in geotextiles for stabilising roads and dams.
Oerlikon Barmag, a division of the Oerlikon Group's Manmade Fibers Segment, is a specialist in the manufacturing of equipment for the production of such fibres and with its high level of technological expertise in the production and handling of synthetic materials, the company has recently enabled a customer in Egypt to establish itself in the growing market for bottle grade granulate by constructing a plant from planning to commissioning.
A consortium of Indian and Egyptian investors recently decided to establish themselves in this growth market. The target of the Egyptian Indian Polyester Company (EIPET) was to set up a facility manufacturing granulate for synthetic bottles in Egypt, with a capacity of 1500 tons per day.
Oerlikon Barmag was able to optimally cover EIPET's needs and worldwide, the Manmade Fibers Segment has completed three polycondensation facilities with a total of seven production lines. In two of these projects, the segment acted as general contractor.
“As this practical material is very much in demand for textiles as also for packaging, many companies are investing in the expansion of production capacities,” said Michael Scholtz, Project Manager at Oerlikon Barmag in Remscheid.
PET is obtained from organic raw materials using a multistep chemical process. Here, terephthalic acid and ethylene glycol are mixed with certain additives to generate a reaction. The high temperatures and vacuum generated within these so-called polycondensation plants transform the raw materials into polymers.
As the technology used in the manufacturing of bottle granulates is largely identical with that used for manmade fibres, Oerlikon benefited from its know-how from this sector when engineering the plant.
With a special technology developed by Oerlikon Barmag, the hot steam, generated during the manufacturing process, can be used to produce cold water. “This so-called vapour absorption distiller significantly reduces the plant's energy consumption,” explained Scholz.
The company’s technology is also said to have a high conversion rate – it creates relatively little waste. In addition, the plant technology enables manufacturers to use a certain amount of recycled synthetic material in the production process, resulting in a reduced need for raw materials.
At Oerlikon Barmag, a team of 30 engineers was responsible for the project. The detailed planning was carried out together with an engineering company in India.
All the components, such as reactors, filters, heating elements, vacuum systems, piping, valves, sensors and control units, were procured from suppliers in various countries. During the subsequent building phase, up to 700 specialists worked on the site. The turnkey plant was handed over to EIPET at the beginning of 2014.
Business intelligence for the fibre, textiles and apparel industries: technologies, innovations, markets, investments, trade policy, sourcing, strategy...
Find out more