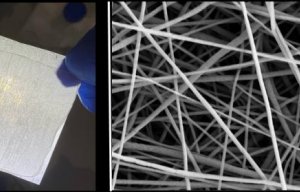
Testing with real coronavirus
A new spin on an old technology will give scientists and manufacturers the ability to significantly increase their production of nanofibres, according to researchers at North Carolina State University. "Collections of nanofibres, because they are porous and lightweight, are useful in applications ranging from water filtration to tissue regeneration to energy storage. But although nanofibres are relatively inexpensive to pro
11th August 2011
Innovation in Textiles
|
Raleigh, NC
A new spin on an old technology will give scientists and manufacturers the ability to significantly increase their production of nanofibres, according to researchers at North Carolina State University.
"Collections of nanofibres, because they are porous and lightweight, are useful in applications ranging from water filtration to tissue regeneration to energy storage. But although nanofibres are relatively inexpensive to produce, the current method of production - needle electro spinning - is time-intensive," NCSU's researchers say, explaining:
"In electro spinning, a liquid-polymer solution is passed through a hypodermic needle held at high voltage. The needle transfers electric charge, which transforms the solution into a jet of charged liquid that "spins" into a nanofibre as it exits the needle. Unfortunately, this method of production does not lend itself to large-scale manufacturing processes."
NC State physicists Laura Clarke and Jason Bochinski, textile engineer Russell Gorga and graduate student Nagarajan Thoppey say they found a particularly simple technique that scales up nanofibre production and provides a close connection to the needle electro spinning method. In a study recently published in the journal Nanotechnology, they demonstrated their so called ‘bowl electro spinning.'
In place of a hypodermic needle, the researchers filled a bowl with the polymer fluid and applied a short burst of very high voltage to the liquid's surface, which caused multiple jets to form and ‘spin' nanofibres onto a collector placed around the outside of the bowl.
According to Bochinski, the experiment gave them a 40-fold increase in nanofibre production, and demonstrated the potential for further increases. It also led to one question that they hope to answer in the near future:
"One of our next steps will be studying the limitations of the bowl apparatus we used - for instance, why was the increase only 40-fold and not 40,000-fold - and how that relates to the geometry of the arrangement and the fluid's properties," Bochinski says.
The work was funded by the National Science Foundation and NC State's Faculty Research and Professional Development Fund. The Department of Physics is part of NC State's College of Physical and Mathematical Sciences. The Department of Textile Engineering, Chemistry and Science is part of NC State's College of Textiles.
An abstract of the paper follows:
"Edge electro spinning for high throughput production of quality nanofibres"
Authors: N M Thoppey, J R Bochinski, L I Clarke and R E Gorga, North Carolina State University
Published: July 29, 2011, in Nanotechnology
A novel, simple geometry for high throughput electro spinning from a bowl edge is presented that utilizes a vessel filled with a polymer solution and a concentric cylindrical collector. Successful fibre formation is presented for two different polymer systems with differing solution viscosity and solvent volatility. The process of jet initiation, resultant fibre morphology and fibre production rate are discussed for this unconfined feed approach.
Under high voltage initiation, the jets spontaneously form directly on the fluid surface and rearrange along the circumference of the bowl to provide approximately equal spacing between spinning sites.
Nanofibres currently produced from bowl electro spinning are identical in quality to those fabricated by traditional needle electro spinning (TNE) with a demonstrated ~40 times increase in the production rate for a single batch of solution due primarily to the presence of many simultaneous jets. In the bowl electro spinning geometry, the electric field pattern and subsequent effective feed rate are very similar to those parameters found under optimized TNE experiments. Consequently, the electro spinning process per jet is directly analogous to that in TNE and thereby results in the same quality of nanofibres.
Business intelligence for the fibre, textiles and apparel industries: technologies, innovations, markets, investments, trade policy, sourcing, strategy...
Find out more