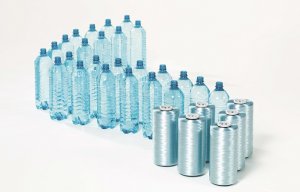
Starlinger’s expanded range at ITMA 2019
Opinion
Anne Prahl reviews the 10th Future Fabrics Expo, held recently in London.
7th July 2022
Anne Prahl
|
London
The 10th Future Fabrics Expo, held on the 28th and 29th of June in London, presented an extensive selection of commercially available fabrics to provide alternatives to conventional high environmental impact materials.
In addition, the expo showcased emerging and speculative fabrics and technologies in the innovation hub and curated area of solutions, which focussed on materials created from agricultural waste and other bio-based ingredients, as well as promoting plastic-free fashion and the integration of biodiversity preservation and regenerative agriculture practices.
The journey to circularity
The fashion industry has to drastically reduce the use of virgin oil-based synthetics such as polyester and nylon and one of the first steps is the adoption of recycled fabrics, as these are generally considered to have a lower environmental impact. While industry is increasingly adopting recycled synthetics, it must be noted that most of these are made from discarded plastic bottles and other plastic waste, rather than pre or post-consumer textile waste.
Environmental organisation and global collaboration network Parley for the Oceans has been one of the success stories in this space and is working with brands including adidas, Dior and Byborre to prevent plastic from entering the oceans and transforming it into sportswear and fashion. More recently, innovators have turned their attention to post consumer tyre waste, which would otherwise be incinerated. Q-Cycle by Fulgar is a yarn created through the chemically recycling of old tyres, which involves breaking down the material into its chemical components and reprocessing it into new materials.
The next step in the circularity journey is the commercial development and adoption of textile-to-textile recycling technologies, including continued innovation around collection, sorting and chemical and mechanical recycling. Pioneers include Recover, who specialise in mechanically recycled cotton fibre and cotton fibre blends and Circ, who use a hydrothermal recycling technology involving water, pressure and responsible chemistry, to turn cotton, polyester and poly-cotton blended post-consumer textiles into new raw materials. Infinited Fiber Company and Renewcell specialise in the manufacture of materials from upcycled cellulosic plant or textile-based waste, while these materials can also be recycled again at end-of-life.
As discussed in the panel discussion ‘Building pathways to circular textile systems’, until recently the economics of textile collection and recycling have been a big challenge, but the current surge in investment into textile-to-textile recycling technologies should bring commercialisation one step closer. However, as Cyndi Rhoades from Worn Again Technologies pointed out, synthetic and blended textile-to-textile recycling is a long-term endeavour and only likely to fully replace the use of virgin fibres within 20-30 years from now.
Alternative feedstock and bio-fabricated solutions
The fashion industry’s dependence on oil-based synthetics and urgent need to diversify what Future Fabrics Expo describes as the ‘future fibre basket’ is driving unprecedented levels of material experimentation and innovation. This trend is further driven by the growing ‘plastic-free’ fashion movement, which sees companies like Natural Fiber Welding pioneering new manufacturing processes and material chemistry to provide a viable and scalable plastic-free fabric future.
The innovation hub and curated solutions area showcased bio-fabricated materials made from algae, bacteria, yeast and mycelium and promoted agricultural waste as an important feedstock for the future. While the Laudes Foundation highlighted outcomes from their report ‘Spinning Future Threads’, which explores how agricultural waste, such as banana pseudo-stem, sugarcane waste, wheat straw, pineapple leaves and rice straw can provide viable fibre feedstock for sustainable textile production at scale, fabrics like Pinatex, Bananatex and Agraloop BioFibre already utilise some of these fibres commercially.
Material science company saltyco’s BioPuff is a fill material made from 70% peatland plant fibre clusters and 30% structurally enhanced BioPuff polymer. Offered as an alternative to animal or petroleum derived products, the material utilises plants grown with regenerative agricultural practices, a process that restores damaged peatlands.
AltMat is an alternative materials science company building regenerative technologies to create future materials by upgrading agricultural residues into high performing natural materials. The company’s Altag is a commercially available cellulose material derived from the agricultural waste of food, medicine and other non-textile crops.
Conceptual and experimental materials displayed in the innovation hub attracted much attention due to their appealing aesthetics and carefully considered sustainability attributes. Textile designer Saumya Singh’s Aeggis material is made by transforming eggshell waste into filaments. These are combined and woven with local British Shetland sheep wool, while colours are derived from kitchen food waste, including tea leaves, chilli powder and onion skins.
Textile designer Jess Redgrave utilises sunflowers to create materials and pigments, as sunflowers can be grown without fertilisers, can be companioned and rotated with other food crops and promote healthy soils due to their roots’ symbiotic relationship with microbes, bacteria and fungi.
Scarlett Yang is a multidisciplinary designer, specialising in tactile fashion, art and material innovation. Yang’s ORI SERI material is a glass-like textile crafted from algae extract and silk cocoon bio waste, which is a by-product of textile manufacturing.
Rediscovering traditional materials
In order to demonstrate how fashion can support biodiversity and develop a more diverse portfolio of materials, special attention was paid to forgotten plant and animal fibres (linen, hemp, ramie, yak and alpaca), reinvented classics (wool, silk, cashmere, cotton) and wild fibres, such as nettle.
Steiff Schulte has been producing three-dimensional pile fabrics since the beginning of the 20th century and is a supplier to the world-famous Steiff toy company. Their manufacture of faux fur utilises natural mohair and alpaca wool fibres and their pile fabrics are made from diverse fibres including hemp, bamboo, paper, linen, soya wool and cotton.
CORKonLINEN is a PU and PVC free leather alternative and is made by applying FSC certified sliced cork to a linen textile backing together with natural, water-based glue. The material is produced in Europe and fully home compostable.
Brazilian sustainable materials company AMADEU offers a wide selection of wild rubber skins and rubberised fabrics and yarns from the Amazon rainforest and other parts of Brazil. The company supports local communities, small producers and artisans by collaborating on material production and initiating research for social innovation. The company has recently launched a new line of materials that mimics leather, combining 100% natural rubber and 100% cotton twill.
Speculative material projects that stood out included Nettle Positive by Eva Pujol, an exploration of Himalayan nettle dyed with microorganisms and bacteria, and Inflaxuation by CQ Studio, which utilises flax, oats, potatoes, natural dye pigments and crustacean shell waste to create leather and fur like materials.
Bio-based dyes and chemistry
Another important spotlight was on fabric dyeing, printing and finishing treatments, as these aspects significantly affect a fabric’s sustainability attributes during manufacture, use and end-of-life.
Substantial investments in biotechnology start-ups such as Colorifix, Beyond Surface Technologies and Living Ink Technologies have already had a positive impact, as we are witnessing a diverse range of bio-based solutions entering the market. While Colorifix utilise microorganisms to grow pigments via on-site fermentation, Beyond Surface Technologies rely on micro algae to produce bio-based wicking finishes for performance sportswear. Living Ink transforms algae by-product material into small, black pigments, which can be produced in dry powder or liquid pigment to provide a bio-based and safe carbon black alternative.
Textile industry start-up SAGES makes 100% natural dyes from food waste, including red cabbage, blueberries and onionskins, which are transformed into powder pigments that can be used as textile dyes. The company is currently developing a natural fixative, in order to be able to match the performance of synthetic dyes.
Material designer Charlotte Werth’s work explores the unique aesthetics achieved by growing pigment-producing bacteria directly on the textile and her bacteria dye machine is capable of producing consistent patterns for scaling up and automating this process.
Future Fabrics Expo showcased an inspiring selection of market-ready, emerging and future-facing solutions, which demonstrate that the material revolution is gathering unstoppable momentum. However, at this exciting time it is critical that innovators consider any potentially negative long-term implications that could arise from working with new types of materials and processes, as well as assuring that their innovations provide scalable and impactful solutions for the most problematic types of fashion materials, such as oil-based synthetics.
Business intelligence for the fibre, textiles and apparel industries: technologies, innovations, markets, investments, trade policy, sourcing, strategy...
Find out more