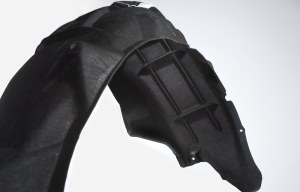
Autoneum’s Re-Liner nominated for 2023 PACE Award
Benefits for hygiene, geotextiles and automotive applications.
6th April 2022
Innovation in Textiles
|
Wielsbeke, Belgium
Beaulieu Fibres International (BIG), based in Wielsbeke, Belgium, highlighted a number of polyolefin and bicomponent developments aimed at advancing sustainable design at the recent IDEA nonwovens show in Miami.
From June 2022, the company will offer ISCC+ certification on polypropylene (PP) and bicomponent PP/polyethylene (PE) fibres. The fibres will be supplied in the range of 1.3-8.9 dtex and will be available in all the main available finish classes – hydrophilic, hydrophobic, etc. – suitable for the main carding and consolidation technologies.
The drop-in solutions – with no loss in quality – will support customers looking to reduce reliance on virgin fossil carbon in their nonwoven and engineered fibre applications.
For hygiene nonwovens, Meralux fibres provide significant sustainable design advantages by enabling around 55% savings in raw materials, with equivalent carbon emission savings. The emission savings are thanks to weight reduction in nonwovens with the same coverage level and also the higher recyclability of PP/PE compared to bicomponent materials.
For customers in industrial segments like geotextiles, high-tenacity HT8 staple fibres enable customers to achieve nonwovens for construction projects with high mechanical performance but with 15% less weight. The durability of the fibres means that less raw material can be used for a longer service lifetime, supporting more sustainable design in addition to resource reduction.
UltraBond bonding staple fibres replace the need for chemical binders, opening up a path to create 100% PP needlepunched fabrics which meet the same performance requirements as traditional constructions, while reducing the end-of-life environmental impact. The needlepunched fabrics are fully recyclable and allow an improved total cost of ownership and a significant ecological footprint reduction.
BIG’s PP fibres for automotive thermoplastic lightweight composites also offer the most optimal cost-to-performance ratio in needlepunched, compression-moulded composite materials. Car manufacturers and OEMs can rely on a bonding fibre range to help improve mechanical, thermal and functional properties of the composite while reducing weight, ultimately reducing fuel consumption on traditional vehicles or increasing autonomy for e-vehicles.
Business intelligence for the fibre, textiles and apparel industries: technologies, innovations, markets, investments, trade policy, sourcing, strategy...
Find out more