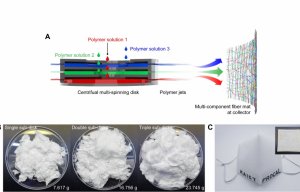
Major gains with centrifugal multispinning
Process employs tandem electrocatalytic and thermocatalytic reactions for the conversion.
17th January 2024
Innovation in Textiles
|
Upton, NY, USA
A research team from the US Department of Energy’s Brookhaven National Laboratory and Columbia University have developed a way to convert carbon dioxide (CO2) into carbon nanofibres with a wide range of unique properties and many potential long-term uses.
The team employs tandem electrochemical and thermochemical reactions running at relatively low temperatures and ambient pressures in a process that could successfully lock carbon away in a useful solid form, to offset or even achieve negative carbon emissions.
“You can, for example, use the carbon nanofibres to strengthen cement that would lock the carbon away for at least 50 years and potentially longer,” said Jingguang Chen, a professor of chemical engineering at Columbia with a joint appointment at Brookhaven Lab, who led the research.
As a bonus, the process also produces hydrogen gas (H2) – a promising alternative fuel.
The idea of capturing CO2 or converting it to other materials to combat climate change is not new, but simply storing CO2 gas can lead to leaks and many CO2 conversions produce carbon-based chemicals or fuels that are used immediately, which releases CO2 right back into the atmosphere.
“We are trying to convert CO2 into something that is value-added but in a solid, useful form,” Chen said. “It’s no simple matter, however, to extract carbon from carbon dioxide and get it to assemble into these fine-scale structures – one direct, heat-driven process requires temperatures in excess of 1,000 degrees Celsius, which is very unrealistic for large-scale CO2 mitigation. By contrast, we have found a process that can occur at about 400 degrees Celsius, which is a much more practical, industrially achievable temperature.”
The trick was to break the reaction into stages and to use two different types of catalysts – materials that make it easier for molecules to come together and react.
“If you decouple the reaction into several sub-reaction steps you can consider using different kinds of energy input and catalysts to make each part of the reaction work,” said Brookhaven Lab and Columbia research scientist Zhenhua Xie.
In a first step, the group used a commercially available electrocatalyst made of palladium supported on carbon and then turned to a heat-activated thermocatalyst made of an iron-cobalt alloy.
“By coupling electrocatalysis and thermocatalysis, we are using this tandem process to achieve things that cannot be achieved by either process alone,” Chen said.
Business intelligence for the fibre, textiles and apparel industries: technologies, innovations, markets, investments, trade policy, sourcing, strategy...
Find out more