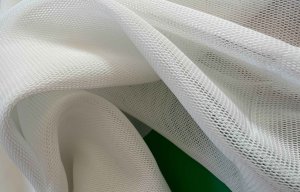
Permanent performance with new Baltex spacer
According to leading warp knitting machine builder Karl Mayer, technical textiles are no longer simply materials, but they are rapidly becoming ready-to-use components. The German company says that the manufacturing sector is increasingly following this trend by developing tailor-made solutions which are aimed at minimising costs and processing sequences during production and by integrating as many functions as possible into the design of the product from the o
1st October 2009
Innovation in Textiles
|
Obertshausen
According to leading warp knitting machine builder Karl Mayer, technical textiles are no longer simply materials, but they are rapidly becoming ready-to-use components. The German company says that the manufacturing sector is increasingly following this trend by developing tailor-made solutions which are aimed at minimising costs and processing sequences during production and by integrating as many functions as possible into the design of the product from the outset. The same trend is also being seen in other knitting technologies such flat knitting and seamless circular knitting where garments and other items such as seat covers are produced in one piece with integrally knitted functional features.
Product developers at Karl Mayer are showing how warp-knitted spacer fabrics can greatly reduce the distance between the machine and the end product. The company’s engineers have developed processes for manipulating the typical characteristics of 3D fabrics, such as their compression elasticity and breathability, and have perfected the machine technology to enable pile-free zones to be produced. The zones without spacer can be arranged as channels in the transverse direction to the processing direction, or alternatively they may alternate with zones having spacers to produce chessboard patterns in the fabric.
Karl Mayer’s warp knitting specialists have now taken another successful step along the road to process-integrated production by manufacturing so called HighDistance materials, which have contours that match the shape of the end product.
Important characteristics for using spacer fabrics in their normal end-uses, for example seats and beds, are their stability under the influence of pressure and how efficiently they deal with moisture. Their breathability can be manipulated by incorporating different patterns in the outer faces of the spacer structures. Constructions which have different opening widths can also be produced and these can be arranged all over the surface in an alternating arrangement or at the sides, depending on the drawing-in arrangement of the ground guide bars.
The monofilament yarns between the cover faces are responsible for the compression stability. In particular, the number per unit of area (which is the result of the stitch number setting), the count and the laying angle have a decisive effect on the cushioning characteristics of the spacer textiles. Furthermore, the compression stability can either be set so that it is constant over the entire textile or so that it varies from zone to zone.
3D warp-knitted fabrics consist of two-dimensional ground faces produced by a plain jersey construction, with a pile layer lying in-between produced by a 1 x 1 rib knitted construction. By selectively integrating the pile yarns into the ground sides, the lappings for the 2D and 3D elements are changed sequentially. The zones without spacers can be arranged in two ways, as stripes in the form of channels and specific flexing points or as square segments alternating with full spacer zones. This variant increases the deployable radius of the 3D warp-knitted textiles considerably.
Extensive research carried out at Karl Mayer on HighDistance materials have led to some promising results when developing products which have contours that match the final application, on the machine itself. The technical concept of the innovative HDR 6 EL high-speed, double-bar raschel machine makes it the perfect machine for producing textiles which have specific end-use characteristics, Karl Mayer says.
The technical features of the machine enable it to produce tailor-made products, where the spacer height can be continuously adjusted centrally from 20 to 65 mm via an electro-motor, and the stitch comb is adjusted automatically when the distance between the knock-over bars is changed. The machine also features patented electronic guide bar control and electronically controlled fabric take-down.
The HighDistance machine is therefore extremely flexible in terms of the structures it can produce and the pile yarns it can process. The pile yarns are laid by means of two guide bars, whose positions can be changed in relation to each other, enabling the laying density to be specified per unit of surface area. Reducing the distance between the pile guide bars via the lapping reduces the 3D segment width and vice versa. Consequently, warp-knitted spacer textiles having perfectly formed circular, layered, wavy or oval contours can be produced. The edges of the spacer textiles are clean and neat with firmly anchored pile yarns. The Multispeed system enables the stitch number to be adjusted so that any compression of the yarns in the pile zone can be more or less equalised.
In addition to the wide range of different contours that can be created, circular and oval shapes without pile yarns can also be produced in the middle of the fabric by varying the distance between the pile bars.
Karl Mayer concludes that all of the different design possibilities offered by the HighDistance machine have turned textile manufacturers into component providers and textile roll goods into piece goods.
Business intelligence for the fibre, textiles and apparel industries: technologies, innovations, markets, investments, trade policy, sourcing, strategy...
Find out more