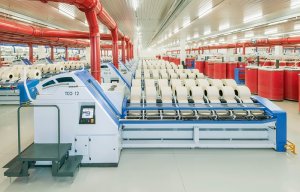
Truetzschler takes over combing business from Toyota
Double-sided drive concept and high-performance drafting system the keys to 50% increase in productivity.
5th September 2023
Innovation in Textiles
|
Moenchengladbach, Germany
For many decades, eight heads on a cotton combing machine have been considered state-of-the-art in the spinning industry, but
Truetzschler’s new heavy duty TCO 21XL comber incorporates 12, to maximise productivity without compromising on quality and also save space in the mill.
Increasing the number of combing heads by 50% makes it possible to achieve production rates of up to 150 kg/h enabling companies who buy and operate two machines instead of three to achieve significant benefits in terms of price-performance-ratio (cost/kg).
Savings can be even more substantial if the machine is operated with Jumbo cans with a diameter of 1,200mm, making it possible to minimise non-productive time when changing the cans.
The double-sided drive concept of Dual Drive and 2Twin Drive ensures the synchronized movement of all machine parts over the entire increased shaft length. During the combing process, high-precision movements are essential to achieve high quality in the sliver. Conventional combers only provide one-sided drives, which lead to higher shaft torsion over the machine width. This might work when operating eight combing heads, but not with four more.
The production 12 slivers is a lot more material for the drafting system to handle and Truetzschler’s high-performance drafting system delivers a decisive advantage because it is specifically designed for processing the increased production volumes. The lower deflection angle at the transition to the web guide protects the highly sensitive combed web, fibres are guided precisely and slivers with excellent levels of uniformity are the result. In the wide drafting system, the minimal bearing temperatures of the top rollers make an important contribution by enabling lower process temperatures during drafting, as well as optimal running behaviour.
Truetzschler has also improved on its tried-and-tested monitoring system by adding an online noil monitoring function to the TCO 21XL, working in combination with the count control function to provide full control over the combing process and the final yarn quality. Variations in the noil are detected automatically and operators receive a warning if any significant change occurs. As a result, the noil percentage and final yarn quality stay consistent. Material distinctions between different lots are also noticed in real-time, which empowers the operator to act quickly. This can enable big savings in material costs, while also reducing the workload of downstream processing.
Business intelligence for the fibre, textiles and apparel industries: technologies, innovations, markets, investments, trade policy, sourcing, strategy...
Find out more